In today’s rapidly evolving industrial landscape, the success of any engineering system hinges on three fundamental pillars: Reliability, Availability, and Maintainability (RAM). As organizations face increasing pressure to optimize operations, reduce costs, and maintain competitive advantages, RAM analysis has emerged as not just a technical framework, but a critical business imperative.
RAM analysis represents the intersection of design excellence, operational efficiency, and maintenance optimization. It provides organizations with a structured approach to ensure their systems perform consistently, remain accessible when needed, and can be efficiently maintained throughout their lifecycle. In an era where unplanned downtime can cost companies millions and customer expectations for reliability are higher than ever, mastering RAM has become essential for survival and success in the industrial sector.
Table of Contents
- 1. Introduction to RAMS
- 2. Understanding RAM Components
- 2.1 Reliability
- 2.2 Availability
- 2.3 Maintainability
- 3. The Interconnected Nature of RAM
- 4. Modern RAM Analysis Implementation
- 5. Industry-Specific Applications
- 6. Optimization Strategies
- 7. Future Trends and Developments
- 8. Best Practices and Guidelines
- 9. Achieving Effective RAM Outcomes: A Five-Step Implementation Guide
- 9. Conclusion
1. Introduction to RAMS
What makes RAM analysis particularly relevant in 2025 is its evolution beyond traditional manufacturing settings. From renewable energy installations to automated logistics systems, from smart cities infrastructure to aerospace applications, RAM principles are being applied across an unprecedented range of industries and technologies. The integration of artificial intelligence, real-time monitoring systems, and predictive analytics has transformed RAM from a reactive measurement tool into a proactive strategic asset.
However, understanding RAM is more than just tracking metrics or implementing maintenance schedules. It’s about recognizing the delicate balance between these interconnected components and how they collectively impact system performance, operational costs, and ultimately, business success. A well-implemented RAM strategy can dramatically reduce maintenance costs, optimize spare parts inventory, extend equipment lifetime, and significantly improve overall system performance.
As we delve deeper into this comprehensive guide, we’ll explore how modern organizations are leveraging RAM analysis to drive operational excellence, enhance decision-making, and create sustainable competitive advantages in an increasingly complex industrial environment.
Recommended Further Reading Amazon Books2. Understanding RAM Components
The foundation of effective system performance lies in understanding the three core components of RAM analysis. Each element plays a distinct yet interconnected role in ensuring optimal system operation. Let’s explore each component in detail:
2.1 Reliability
- Reliability represents the probability of system operation without failure under specific conditions and timeframe
- Measured through established metrics like MTBF (Mean Time Between Failures) and MTTF (Mean Time To Failure)
- Critical for predictability and consistent system performance
- Forms the basis for preventive maintenance scheduling and resource allocation
Reliability is fundamentally about consistency and predictability in system performance. It answers the crucial question: “How likely is it that our system will perform its intended function without failing?” In modern industrial settings, reliability is measured using sophisticated tools and methodologies:
- FMEA (Failure Modes and Effects Analysis)
- Identifies potential equipment damage before occurrence
- Analyzes causes and consequences of failures
- Calculates Risk Priority Numbers (RPN) to prioritize interventions
- Helps maintenance teams focus on critical failure points
- Fault Tree Analysis (FTA)
- Provides logical reconstruction of failure pathways
- Identifies physical, human, and latent root causes
- Enables understanding of system tolerance to single or multiple failures
- Supports proactive maintenance planning
- Reliability Block Diagrams (RBD)
- Maps component relationships and dependencies
- Visualizes failure impact pathways
- Supports system optimization decisions
- Helps identify critical reliability bottlenecks
2.2 Availability
- Measures system readiness to perform intended functions at any given time
- Combines impacts of both reliability and maintainability
- Directly affects operational efficiency and productivity
- Critical for service level agreement compliance
Availability is perhaps the most visible RAM component to business operations. It represents the percentage of time a system is actually operational and capable of performing its intended functions. Modern availability calculations take into account:
- Planned maintenance windows
- Unplanned downtimes
- Setup and adjustment times
- Quality losses and reduced speed operation
- Environmental and operational constraints
2.3 Maintainability
- Reflects the ease and speed of system restoration after failure
- Measured primarily through Mean Time To Repair (MTTR)
- Influenced by design factors and maintenance resource accessibility
- Critical for minimizing downtime and operational disruption
Maintainability focuses on the practical aspects of keeping systems operational. In 2025’s context, maintainability has evolved to include:
- Accessibility of components for repair and inspection
- Availability of diagnostic tools and information
- Integration with predictive maintenance systems
- Resource requirements for maintenance activities
- Safety considerations during maintenance operations
Metric | Formula | When to Use | Target Values | Common Pitfalls |
---|---|---|---|---|
MTBF | Operating Time / Number of Failures | System reliability assessment | Industry-specific | Not excluding planned downtime |
MTTR | Total Repair Time / Number of Repairs | Maintainability analysis | < 4 hours (typical) | Overlooking setup time |
Availability | MTBF / (MTBF + MTTR) × 100% | Overall system performance | >95% (typical) | Not considering all downtime types |
Reliability | e^(-time/MTBF) | Failure probability analysis | Application-specific | Using incorrect time periods |
OEE | Availability × Performance × Quality | Overall equipment effectiveness | >85% (world-class) | Incomplete data collection |
Understanding these components in isolation is important, but their true value emerges when we consider their interconnected nature and how they collectively impact system performance. Modern RAM analysis requires balancing these elements while considering both technical requirements and business objectives.
The successful implementation of RAM principles depends on proper measurement and monitoring of these components through appropriate metrics and tools. As we’ll explore in later sections, advanced technologies and analytical approaches have transformed how organizations track and optimize these crucial elements of system performance.
Recommended Further Reading Amazon Books3. The Interconnected Nature of RAM
The relationship between reliability, availability, and maintainability is far more complex than a simple three-part system. These components form an intricate web where changes to one element inevitably impact the others, creating both challenges and opportunities for system optimization.
- RAM components create a dynamic system of trade-offs
- System-level optimization requires balanced decision-making
- Modern technology enables better performance monitoring
- Cost considerations drive optimization choices
Understanding the Trade-offs
Consider a manufacturing plant that increases system reliability by implementing sophisticated fault tolerance mechanisms. While this might reduce the frequency of failures, it could simultaneously make the system more challenging to maintain. Maintenance technicians now require specialized training, repairs take longer, and spare parts become more expensive. This scenario perfectly illustrates how improving reliability can potentially decrease maintainability and, during maintenance periods, reduce availability.
Conversely, simplifying maintenance procedures to improve maintainability might compromise system reliability. A streamlined maintenance checklist might speed up repairs but could lead to oversight of critical inspection points, potentially increasing the likelihood of future failures.
The Cost-Performance Balance
The interconnected nature of RAM becomes particularly evident when considering cost implications. High-reliability components typically command premium prices, impacting initial system costs. However, they might reduce maintenance frequency and extend system life, potentially lowering long-term operational costs. This balance between upfront investment and ongoing operational expenses represents a critical decision point for organizations.
Modern Optimization Approaches
In 2025, organizations are leveraging advanced technologies to better manage these interconnections. Real-time monitoring systems and predictive analytics help maintenance teams anticipate potential failures before they occur. This proactive approach helps balance the reliability-maintainability equation by enabling targeted interventions that minimize system disruption.
Digital twin technology allows organizations to simulate different RAM scenarios, understanding the ripple effects of changes before implementation. This capability has transformed how companies approach system optimization, enabling more informed decision-making about maintenance strategies and system modifications.
Business Impact
The interconnected nature of RAM directly affects business performance through multiple channels. Production efficiency, customer satisfaction, and operational costs all depend on finding the right balance between these components. Organizations must consider both technical requirements and business objectives when optimizing their RAM strategy.
Understanding these relationships is crucial for developing effective maintenance strategies and achieving optimal system performance. As we’ll explore in subsequent sections, modern technologies and methodologies are providing new ways to manage these interconnections effectively, enabling organizations to achieve better overall system performance while controlling costs.
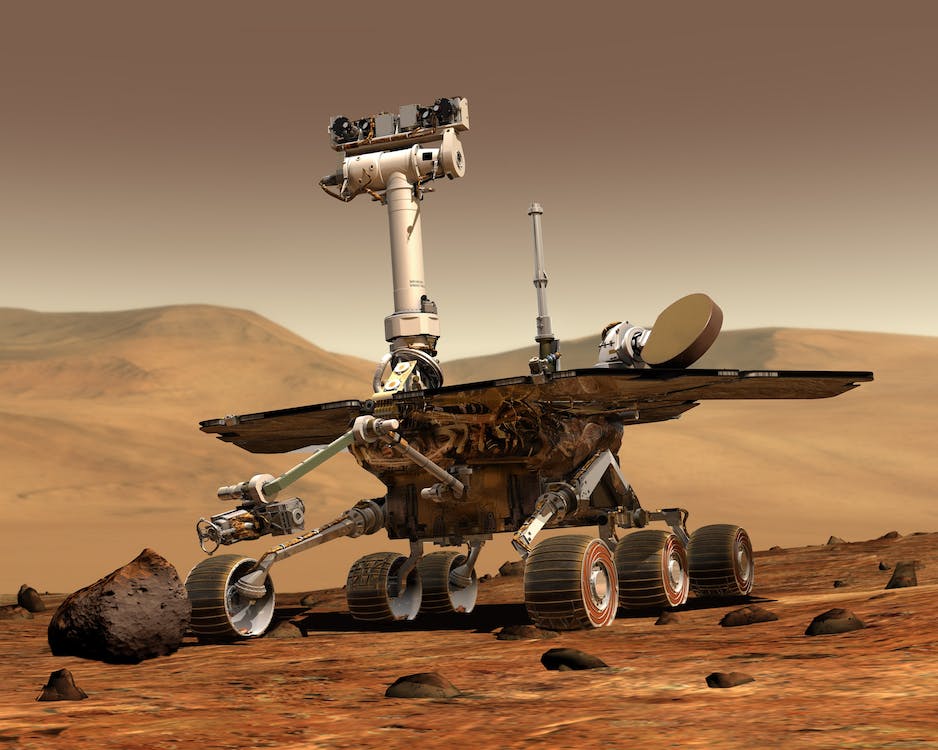
4. Modern RAM Analysis Implementation
The implementation of RAM analysis has undergone a revolutionary transformation in the digital age. What began as a reactive process based on historical data has evolved into a dynamic, real-time approach that leverages advanced technologies and Industry 4.0 principles. Digital transformation has revolutionized how we collect and analyze data, real-time monitoring enables truly proactive maintenance, sophisticated data analytics drives decision-making, and seamless integration with Industry 4.0 systems enhances overall implementation effectiveness.
Digital Tools and Real-Time Monitoring
Modern RAM analysis relies heavily on advanced monitoring systems that provide continuous insight into system performance. Smart sensors and IoT devices now collect data on everything from vibration patterns to temperature fluctuations, enabling early detection of potential failures. This continuous monitoring has fundamentally changed how organizations approach maintenance scheduling and resource allocation.
For example, a modern manufacturing facility might employ wireless sensors across its production line, tracking key performance indicators in real-time. These sensors feed data into centralized analytics platforms, which can identify patterns and anomalies that might indicate impending equipment failure. This capability has dramatically improved both reliability predictions and maintenance planning.
Advanced Analytics in Practice
The true power of modern RAM implementation lies in its analytical capabilities. Machine learning algorithms now process vast amounts of operational data, identifying subtle patterns that might escape human observation. These insights enable maintenance teams to move beyond traditional scheduled maintenance to more sophisticated predictive and prescriptive approaches.
Consider a power generation facility using advanced analytics to optimize its maintenance schedule. The system might analyze thousands of data points across multiple parameters, considering factors such as equipment age, operating conditions, and historical performance patterns. This analysis helps determine optimal maintenance timing, balancing the need for reliability with operational efficiency.
Integration with Existing Systems
Successful RAM implementation in 2025 requires seamless integration with existing enterprise systems. Modern CMMS (Computerized Maintenance Management Systems) now incorporate RAM analytics directly into their workflows, enabling better coordination between maintenance planning and operational requirements. This integration ensures that RAM analysis isn’t just a theoretical exercise but a practical tool for operational improvement.
The Role of Artificial Intelligence
AI has become instrumental in modern RAM analysis, offering capabilities that extend far beyond traditional statistical approaches. Modern AI systems predict equipment failures with increasing accuracy, optimize maintenance schedules across complex systems, recommend specific maintenance actions based on system conditions, and analyze the effectiveness of maintenance interventions. These capabilities have transformed how organizations approach system reliability and maintenance planning.
Practical Implementation Challenges
Despite these technological advances, organizations still face significant challenges in implementing modern RAM analysis. Data quality remains a crucial concern, as does the need for skilled personnel who can interpret and act on analytical insights. Successful implementation requires a balanced approach that combines technological capabilities with practical operational expertise.
The key to successful modern RAM implementation lies in understanding that technology alone isn’t the answer. Organizations must develop comprehensive implementation strategies that consider both technical capabilities and human factors, ensuring that new tools and approaches enhance rather than complicate existing processes.
Recommended Future Learn Short Courses5. Industry-Specific Applications
RAM analysis principles find unique expressions across different industries, each adapting the framework to meet their specific operational demands and regulatory requirements.
Manufacturing Sector
In modern manufacturing, RAM analysis focuses heavily on production line optimization. Smart factories employ continuous monitoring systems that track equipment performance in real-time. Predictive maintenance algorithms analyze vibration patterns, temperature variations, and power consumption to forecast potential failures before they occur. This approach has significantly reduced unplanned downtime and improved overall equipment effectiveness (OEE).
Energy and Utilities
Power generation and distribution systems require exceptional reliability due to the critical nature of their service. Energy companies implement sophisticated RAM strategies that account for both equipment performance and grid stability. Modern power plants use advanced sensors and analytics to monitor turbine performance, while smart grid systems automatically reroute power distribution to maintain service reliability.
Transportation and Logistics
Airlines and railway operators prioritize safety and punctuality through comprehensive RAM programs. Aircraft maintenance schedules are optimized using real-time performance data from thousands of sensors, while railway systems employ predictive analytics to prevent track and rolling stock failures. The integration of IoT devices has enabled more precise monitoring of vehicle fleets and infrastructure components.
Aerospace and Defense
The aerospace sector demands the highest levels of reliability due to safety-critical operations. RAM analysis in this industry focuses on component lifecycle management and system redundancy. Modern aircraft employ sophisticated health monitoring systems that provide real-time performance data, enabling maintenance teams to address potential issues before they affect operational safety.
Chemical Processing
Chemical plants require strict adherence to safety protocols while maintaining production efficiency. RAM analysis in this sector focuses on preventing equipment failures that could lead to hazardous situations. Advanced monitoring systems track chemical processes in real-time, while predictive analytics help optimize maintenance schedules without compromising safety standards.
These industry applications demonstrate how RAM analysis adapts to specific operational contexts while maintaining its core principles of optimizing reliability, availability, and maintainability. The key to success lies in understanding industry-specific requirements and tailoring RAM strategies accordingly.
6. Optimization Strategies
Effective RAM optimization requires a systematic approach that balances technical requirements with business objectives. Modern organizations are moving beyond traditional maintenance approaches to embrace data-driven optimization strategies.
Essential RAM Optimization Checklist:
- Initial Assessment
- Document current system performance metrics
- Identify critical failure points
- Map maintenance resource allocation
- Review historical failure patterns
- Strategy Development
- Define performance targets
- Establish monitoring protocols
- Allocate resources effectively
- Create implementation timeline
- Implementation Plan
- Deploy monitoring systems
- Train maintenance personnel
- Establish reporting procedures
- Set up feedback mechanisms
Cost-Benefit Considerations
Cost optimization in RAM requires balancing initial investments against long-term operational benefits. Organizations must consider equipment lifecycle costs, maintenance resource allocation, and the impact of downtime on production. Modern approaches leverage predictive analytics to optimize this balance, ensuring that maintenance investments deliver maximum value.
Performance Monitoring
Continuous performance monitoring enables organizations to identify optimization opportunities and track the effectiveness of implemented strategies. Real-time data collection and analysis help maintenance teams make informed decisions about resource allocation and intervention timing.
7. Future Trends and Developments
The evolution of RAM analysis continues to accelerate, driven by technological advances and changing industrial requirements. Understanding emerging trends is crucial for maintaining competitive advantage and operational excellence.
Emerging Technologies Impact List:
- Artificial Intelligence and Machine Learning
- Automated fault detection
- Dynamic maintenance scheduling
- Predictive failure analysis
- Pattern recognition in system behavior
- Internet of Things (IoT)
- Real-time performance monitoring
- Remote system diagnostics
- Automated data collection
- Condition-based maintenance
- Digital Twins
- Virtual system modeling
- Scenario testing
- Performance optimization
- Risk assessment
Integration with Industry 4.0
The convergence of RAM analysis with Industry 4.0 principles is creating new opportunities for system optimization. Smart factories now integrate RAM considerations into their automation systems, enabling real-time adjustments to maintain optimal performance.
Sustainability Considerations
Environmental sustainability has become a critical factor in RAM optimization. Organizations are increasingly considering environmental impact alongside traditional performance metrics, leading to new approaches in system design and maintenance planning.
Machine Learning Applications
Advanced machine learning algorithms are transforming how organizations approach RAM analysis. These systems can now predict potential failures with increasing accuracy, optimize maintenance schedules, and recommend specific interventions based on complex pattern analysis.
The future of RAM analysis lies in the integration of these emerging technologies with proven optimization strategies. Organizations that successfully adopt these innovations while maintaining focus on fundamental RAM principles will be best positioned for future success.
8. Best Practices and Guidelines
Best practices in RAM analysis continue to evolve with technological advancement, yet certain fundamental principles remain crucial for success. Understanding these guidelines helps organizations avoid common pitfalls and maximize the value of their RAM initiatives.
Phase | Key Activities | Required Resources | Success Criteria | Timeline |
---|---|---|---|---|
Planning | Baseline assessment, Goal setting | Analysis software, SMEs | Metrics defined, Team aligned | 1-2 months |
Implementation | System deployment, Training | Monitoring tools, Training staff | Systems operational | 3-6 months |
Monitoring | Data collection, Analysis | Analytics platform, Analysts | Regular reporting established | Ongoing |
Optimization | Performance tuning, Process refinement | Analysis tools, Technical experts | Targets achieved | Continuous |
Review | Assessment, Strategy adjustment | Reporting tools, Management | ROI demonstrated | Quarterly |
9. Achieving Effective RAM Outcomes: A Five-Step Implementation Guide
The path to successful RAM implementation can seem complex, but it can be broken down into five essential steps that any organization can follow. Each step builds upon the previous one, creating a solid foundation for sustainable RAM excellence.
Step 1: Establish Your Baseline
Begin by thoroughly documenting your current system performance. Measure existing downtime, failure rates, and maintenance response times. Identify critical equipment and systems that have the most significant impact on operations. This baseline provides a clear starting point and helps identify priority areas for improvement. Collection of this initial data typically takes 30-60 days to ensure accuracy.
Step 2: Set Clear Performance Targets
Using your baseline data, establish specific, measurable performance goals. Focus on metrics that directly impact business outcomes, such as overall equipment effectiveness (OEE), mean time between failures (MTBF), and maintenance response times. Ensure these targets align with both technical capabilities and business objectives. Your goals should be challenging yet achievable within a 12-18 month timeframe.
Step 3: Implement Monitoring Systems
Deploy appropriate technology solutions to track RAM metrics in real-time. This might include installing sensors on critical equipment, implementing a computerized maintenance management system (CMMS), or setting up performance dashboards. The key is ensuring that data collection is automated, accurate, and accessible to relevant stakeholders. Modern monitoring systems should provide both real-time alerts and trend analysis capabilities.
Step 4: Develop Response Protocols
Create clear procedures for how your organization will respond to different types of performance issues. This includes establishing maintenance triggers, defining escalation paths, and setting up regular review cycles. Train your teams on these protocols and ensure they understand both the technical requirements and business implications of their decisions. Update these protocols based on actual performance data and team feedback.
Step 5: Review and Optimize
Implement a regular review cycle to assess performance against targets and identify opportunities for improvement. This should include monthly operational reviews, quarterly performance assessments, and annual strategic planning. Use data-driven insights to refine your approach continuously. Focus on both quick wins and long-term systematic improvements.
Success in RAM implementation comes from consistent execution of these steps while maintaining focus on your organization’s specific needs and constraints. Regular communication with stakeholders, ongoing team training, and commitment to continuous improvement will help ensure sustainable results.
9. Conclusion
The evolution of RAM analysis represents a fundamental shift in how organizations approach system performance and maintenance. As we look toward the future, several key considerations emerge as critical for success.
Moving Forward
Modern RAM analysis has transformed from a purely technical discipline into a strategic business tool. Organizations that successfully implement RAM principles while embracing technological innovations position themselves for sustainable competitive advantage.
Critical Success Factors
Organizations should focus on:
- Integration of advanced analytics with traditional RAM principles
- Development of comprehensive data collection and analysis capabilities
- Investment in workforce training and development
- Commitment to continuous improvement
- Balance between technical excellence and business objectives
The future of RAM analysis lies in its ability to adapt to changing technological landscapes while maintaining focus on fundamental principles of reliability, availability, and maintainability. Organizations that successfully navigate this balance will find themselves well-positioned for success in an increasingly competitive industrial environment.