In the complex world of systems engineering, ensuring the reliability, efficiency, and safety of technical systems is paramount. This is where RAMS – Reliability, Availability, Maintainability, and Safety – comes into play. RAMS represents a crucial set of quality characteristics that are essential for guaranteeing the dependability and safety of engineered systems across various industries.
This comprehensive guide aims to delve deep into the concept of RAMS, exploring its individual components and their collective importance in systems engineering. We’ll examine how RAMS differs from RAM (Reliability, Availability, and Maintainability), highlighting the critical role that safety plays in this expanded framework.
Throughout this article, we will:
- Explore each component of RAMS in detail
- Clarify the distinction between RAM and RAMS
- Provide a tabulated overview of key considerations and mitigations in RAMS integration
- Discuss critical issues that arise in RAMS implementation
- Analyze scenarios where safety should take precedence
- Present real-world examples of RAMS integration across various engineering sectors
- Offer best practices for effectively integrating RAMS into systems engineering processes
By the end of this guide, readers will gain a comprehensive understanding of RAMS and its significance in creating robust, efficient, and safe technical systems. Whether you’re a seasoned systems engineer or new to the field, this article will equip you with valuable insights to make informed decisions in system design, implementation, and maintenance.
Table of Contents
- Characteristics of RAMS
- Differentiating RAM and RAMS
- Key Considerations and Mitigations in RAMS Integration
- Critical Issues in RAMS Integration
- When to Prioritise Safety
- Balancing Safety with Operational Efficiency
- Real-World Examples of RAMS Integration Across Engineering Industries
- Best Practices for RAMS Integration in Systems Engineering
- Making Informed Decisions
- Conclusion
Characteristics of RAMS
RAMS is an acronym that stands for Reliability, Availability, Maintainability, and Safety. It incorporates both qualitative and quantitative measures, providing a comprehensive framework for assessing and improving system performance.
Qualitative Measures: Qualitative measures are employed for tasks such as:
- Identifying potential hazards
- Analyzing risks
- Evaluating failure modes and their effects
- Assessing the impact of human factors on system performance
Quantitative Measures: Quantitative measures involve the computation of specific metrics, including:
- Mean Time Before Failure (MTBF): The average time a system operates before experiencing a failure
- Mean Time To Repair (MTTR): The average time required to repair a failed system and restore it to operational status
- Maintenance Ratio (MR): The ratio of maintenance hours to operational hours
These metrics play a pivotal role in evaluating the performance of a system, allowing engineers to:
- Set objective performance targets
- Compare different system designs or configurations
- Monitor system performance over time
- Identify areas for improvement in reliability and maintainability
- Optimize maintenance schedules and resource allocation
By combining qualitative and quantitative approaches, RAMS provides a holistic view of system performance, ensuring that both tangible metrics and intangible factors are considered in system design, operation, and maintenance.
Recommended Further Reading Amazon BooksDifferentiating RAM and RAMS
While RAM (Reliability, Availability, and Maintainability) forms the core of systems engineering, RAMS (Reliability, Availability, Maintainability, and Safety) represents a more comprehensive approach that explicitly incorporates safety considerations. This distinction is crucial for understanding the broader implications of system design and operation.
RAM Focus: RAM primarily concentrates on operational efficiency and system performance. It addresses:
- Reliability: The probability that a system or component will perform its intended function under specified conditions for a certain period.
- Availability: The proportion of time a system is in a functioning condition.
- Maintainability: The ease and speed with which a system can be restored to operational status after a failure.
These aspects are critical for ensuring system uptime, minimizing downtime, and optimizing maintenance processes.
RAMS Expansion: RAMS builds upon the RAM framework by adding the crucial element of Safety. This addition highlights the importance of risk reduction and protection of operators, assets, and the environment. Key aspects of the safety integration include:
- Hazard Identification: Systematic processes to identify potential safety risks.
- Risk Analysis: Evaluating the likelihood and consequences of identified hazards.
- Safety Measures: Implementing controls to mitigate or eliminate safety risks.
- Regulatory Compliance: Ensuring adherence to relevant safety standards and regulations.
Importance of Safety Integration: The inclusion of safety in RAMS acknowledges that system failures can have consequences beyond operational inefficiencies. It recognizes that failures might lead to:
- Harm to human life
- Damage to system assets
- Environmental impact
- Legal and regulatory implications
By incorporating safety into the RAM analysis, engineers can:
- Examine the system more thoroughly, considering both performance and safety aspects
- Create more resilient systems that protect against both operational failures and safety incidents
- Develop a more comprehensive and well-rounded approach to systems engineering
Trade-offs and Considerations: Integrating safety into RAM often requires careful balancing:
- Performance vs. Safety: Sometimes, safety measures might slightly reduce system performance or efficiency.
- Cost Implications: Enhancing safety features may increase initial costs but can lead to long-term savings by preventing accidents and associated liabilities.
- Complexity: Adding safety systems can increase system complexity, which needs to be managed carefully to avoid introducing new failure modes.
RAMS in Practice: To effectively implement RAMS, engineers utilize various tools and techniques, including:
- Failure Mode, Effects, and Criticality Analysis (FMECA)
- Fault Tree Analysis (FTA)
- Reliability Block Diagrams (RBD)
- Human Reliability Analysis (HRA)
- Maintenance Requirements Analysis (MRA)
- Failure Recording Analysis and Corrective Action System (FRACAS)
These tools help in identifying potential failures, their impacts, and mitigation strategies, all while considering both operational efficiency and safety.
Recommended Further Reading Amazon BooksKey Considerations and Mitigations in RAMS Integration
When integrating RAMS principles into systems engineering, several key considerations must be addressed to ensure comprehensive coverage of reliability, availability, maintainability, and safety aspects. The following table provides an overview of these considerations along with potential mitigation strategies:
Consideration | Description | Potential Mitigations |
---|---|---|
System Complexity | As systems become more complex, the likelihood of failures and safety risks increases. | – Modular design approaches – Simplification where possible – Thorough testing of system interactions |
Environmental Factors | Operating conditions can significantly impact RAMS performance. | – Robust design for anticipated conditions – Environmental testing – Adaptive control systems |
Human Factors | Human interaction with the system can introduce reliability and safety risks. | – Human Reliability Analysis (HRA) – User-centered design – Comprehensive training programs |
Redundancy and Diversity | Critical systems may require backup or alternative operational modes. | – Redundant components for critical functions – Diverse systems to prevent common mode failures |
Maintenance Accessibility | Ease of maintenance impacts system availability and safety. | – Design for maintainability – Predictive maintenance strategies – Remote monitoring capabilities |
Obsolescence Management | Long-life systems may face parts becoming obsolete. | – Life cycle planning – Use of standardized components – Regular technology refresh cycles |
Software Reliability | Software failures can impact overall system RAMS. | – Rigorous software testing – Formal verification methods – Regular software updates and patches |
Integration of Legacy Systems | Incorporating older systems with new ones can introduce compatibility issues. | – Thorough interface analysis – Gradual migration strategies – Compatibility testing |
Supply Chain Reliability | The reliability of suppliers affects overall system performance. | – Supplier quality assurance programs – Multiple sourcing strategies – Regular supplier audits |
Regulatory Compliance | Adherence to standards and regulations is crucial for safety and legal reasons. | – Regular compliance audits – Proactive engagement with regulatory bodies – Design with compliance in mind |
Data Management and Analysis | Effective RAMS requires robust data collection and analysis. | – Implement FRACAS – Use of data analytics for predictive maintenance – Regular RAMS performance reviews |
Life Cycle Costs | RAMS considerations impact costs throughout the system’s life cycle. | – Life cycle cost analysis – Trade-off studies between reliability and cost – Value engineering approaches |
Emergency Response and Recovery | Planning for potential failures and safety incidents is essential. | – Develop comprehensive emergency procedures – Regular drills and simulations – Robust backup and recovery systems |
This table provides a foundation for systematically addressing RAMS considerations in systems engineering. By proactively considering these factors and implementing appropriate mitigations, organizations can enhance the overall reliability, availability, maintainability, and safety of their systems.
It’s important to note that the specific considerations and mitigations may vary depending on the nature of the system, its operating environment, and applicable industry standards. Regular review and updating of these considerations throughout the system’s life cycle is crucial for maintaining effective RAMS integration.
Critical Issues in RAMS Integration
While integrating RAMS principles into systems engineering offers numerous benefits, it also presents several critical issues that need to be addressed. These issues can significantly impact the success of RAMS implementation and the overall performance of the system. Here are some of the key challenges:
- Balancing Trade-offs: One of the most significant challenges in RAMS integration is balancing the often-competing demands of reliability, availability, maintainability, and safety. For instance, improving safety might reduce availability, or enhancing reliability could increase costs. Engineers must carefully weigh these trade-offs to achieve optimal system performance.
- Data Quality and Availability: Effective RAMS analysis relies heavily on accurate and comprehensive data. However, obtaining reliable data, especially for new or innovative systems, can be challenging. Issues include:
- Lack of historical data for novel technologies
- Inconsistencies in data collection methods
- Difficulties in capturing data on rare events or near-misses
- Complexity Management: As systems become more complex, particularly with the integration of software and hardware components, managing RAMS becomes increasingly difficult. This complexity can lead to:
- Unforeseen interactions between components
- Difficulties in identifying all potential failure modes
- Challenges in predicting system behavior under all possible conditions
- Human Factors Integration: Human interaction with systems remains a critical factor in RAMS. Key issues include:
- Accurately modeling human behavior and potential errors
- Designing interfaces that minimize the risk of human error
- Ensuring that safety procedures are followed consistently
- Lifecycle Considerations: RAMS principles need to be applied throughout the entire lifecycle of a system, from conception to decommissioning. Challenges include:
- Maintaining RAMS performance as systems age
- Adapting to changing operational requirements over time
- Managing obsolescence of components and technologies
- Supply Chain Management: The reliability of a system is only as strong as its weakest component. Issues in supply chain management that affect RAMS include:
- Ensuring consistent quality from suppliers
- Managing the risk of counterfeit parts
- Dealing with supply chain disruptions
- Integration with Existing Systems: Many new systems need to integrate with legacy systems, which can present significant RAMS challenges:
- Ensuring compatibility between new and old technologies
- Maintaining overall system reliability when integrating disparate components
- Managing the increased complexity of hybrid systems
- Regulatory Compliance and Standards: Keeping up with evolving regulations and standards across different jurisdictions can be challenging. Issues include:
- Interpreting and applying complex regulatory requirements
- Harmonizing RAMS practices across international boundaries
- Balancing compliance with innovation and efficiency
- Cost Justification: While RAMS integration can lead to long-term cost savings, justifying the initial investment can be challenging. This includes:
- Quantifying the return on investment for RAMS activities
- Balancing short-term costs against long-term benefits
- Convincing stakeholders of the value of RAMS integration
- Continuous Improvement and Adaptation: RAMS is not a one-time implementation but a continuous process. Challenges include:
- Establishing effective feedback loops for continuous improvement
- Adapting RAMS strategies to evolving technologies and operational environments
- Maintaining organizational commitment to RAMS principles over time
Addressing these critical issues requires a multidisciplinary approach, involving not just engineers but also management, operations personnel, and other stakeholders. By recognizing and proactively addressing these challenges, organizations can more effectively integrate RAMS principles into their systems engineering processes, leading to more reliable, available, maintainable, and safe systems.
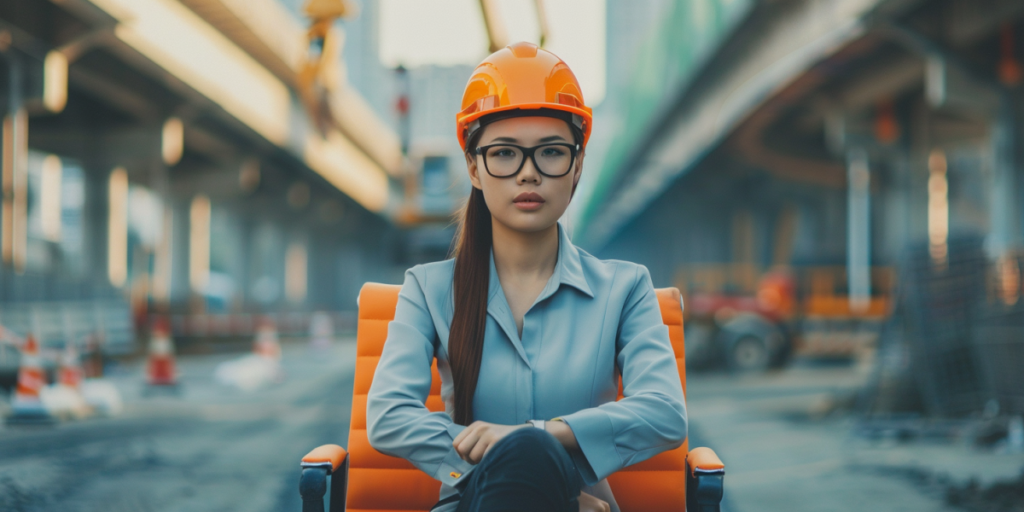
When to Prioritise Safety
While reliability, availability, and maintainability are crucial aspects of system performance, there are scenarios where safety must take precedence. Understanding when and how to prioritize safety within the RAMS framework is essential for creating systems that are not only efficient but also protect human life, assets, and the environment.
Scenarios Requiring Safety Prioritization:
- High-risk environments
- Systems with direct impact on human life
- Processes involving hazardous materials
- Critical infrastructure operations
- Emergency response systems
- Public transportation
- Healthcare technologies
Table 2: RAMS Relevance and Key Criteria Across Industries
Industry | RAMS Relevance | Key Criteria for Reliability/Availability | Key Criteria for Safety |
---|---|---|---|
Defence | Critical for mission success and personnel safety | Equipment readiness System redundancy Harsh environment tolerance | Fail-safe mechanisms Secure communications Personnel protection systems |
Healthcare | Vital for patient care and medical procedures | Equipment uptime Accuracy of diagnostic systems Quick maintenance turnaround | Patient data protection Sterility assurance Radiation exposure control |
Railways | Essential for operational efficiency and passenger safety | On-time performance Rolling stock availability Infrastructure reliability | Collision avoidance systems Emergency braking systems Platform safety measures |
Aviation | Crucial for aircraft operation and passenger safety | Engine reliability Navigation system accuracy Maintenance scheduling | Redundant flight controls Cabin pressurization systems Emergency evacuation procedures |
Nuclear Power | Fundamental for plant operation and environmental safety | Reactor stability Power output consistency Component longevity | Containment systems Radiation monitoring Emergency shutdown procedures |
Oil and Gas | Important for continuous operation and environmental protection | Equipment durability Production efficiency Corrosion resistance | Leak detection systems Pressure relief valves Fire suppression systems |
Automotive | Key for vehicle performance and user safety | Engine durability Fuel efficiency Electronics reliability | Airbag systems Anti-lock braking systems Collision avoidance technology |
Balancing Safety with Operational Efficiency
While prioritizing safety is crucial in many scenarios, it’s important to find a balance with operational efficiency. Here are some strategies to achieve this balance:
- Risk-Based Approach: Implement a risk assessment methodology to identify and prioritize safety measures based on the likelihood and severity of potential hazards.
- Design for Safety: Incorporate safety features into the initial system design rather than adding them as afterthoughts. This approach often leads to more efficient and effective safety measures.
- Performance-Based Safety Standards: Focus on achieving safety outcomes rather than prescriptive rules, allowing for innovative solutions that maintain safety while improving efficiency.
- Continuous Monitoring and Improvement: Implement systems for ongoing monitoring of both safety and operational performance, using data to drive continuous improvements in both areas.
- Training and Culture: Develop a strong safety culture through comprehensive training programs, ensuring that all personnel understand the importance of both safety and operational efficiency.
- Technology Integration: Leverage advanced technologies like AI and IoT to enhance both safety and efficiency simultaneously, such as predictive maintenance systems that improve both reliability and safety.
- Stakeholder Engagement: Involve all stakeholders, including end-users, in the design and implementation of safety measures to ensure they are practical and do not unnecessarily hinder operations.
- Regular Reviews: Conduct periodic reviews of safety measures and operational procedures to identify areas where safety might be over-engineered at the expense of efficiency, or vice versa.
By carefully considering the specific needs of each industry and implementing these balancing strategies, organizations can achieve optimal RAMS outcomes that prioritize safety without unduly compromising operational efficiency. The key is to view safety not as a constraint on performance, but as an integral part of overall system excellence.
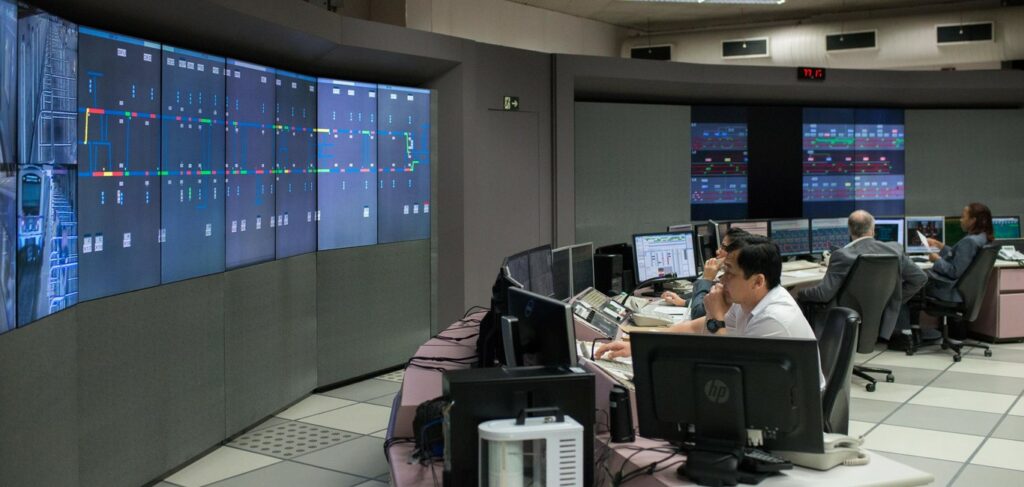
Real-World Examples of RAMS Integration Across Engineering Industries
To illustrate the practical application of RAMS principles, let’s examine some real-world examples from various engineering industries. These cases demonstrate how organizations have successfully integrated RAMS to improve system performance, safety, and overall efficiency.
Railway Signalling Systems
Industry: Transportation RAMS Application: European Train Control System (ETCS)
The European Train Control System is a prime example of RAMS integration in the railway industry. This advanced signaling system enhances safety and increases line capacity.
Key RAMS elements:
- Reliability: Redundant communication channels between trains and control centers
- Availability: Fallback operational modes to ensure continued service in case of partial system failure
- Maintainability: Modular design allowing for easy component replacement and upgrades
- Safety: Automatic train protection features, including emergency braking
Outcome: Improved train punctuality, increased line capacity, and enhanced safety across European rail networks.
Aircraft Engine Design
Industry: Aviation RAMS Application: Rolls-Royce Trent XWB Engine
The Trent XWB engine, used in long-haul aircraft, showcases how RAMS principles can be applied to complex aerospace systems.
Key RAMS elements:
- Reliability: Advanced materials and design to extend time between overhauls
- Availability: Health monitoring systems for predictive maintenance
- Maintainability: Modular design for quick replacement of components
- Safety: Fail-safe systems and containment features for engine blade failures
Outcome: Increased engine lifespan, reduced maintenance costs, and improved safety records for long-haul flights.
Nuclear Power Plant Operations
Industry: Energy RAMS Application: Fukushima Daiichi Nuclear Disaster Response
The Fukushima disaster in 2011 led to significant RAMS improvements in nuclear power plant design and operation worldwide.
Key RAMS elements:
- Reliability: Enhanced backup power systems and cooling mechanisms
- Availability: Improved grid connection reliability and on-site power generation
- Maintainability: Accessible design for critical safety systems even under extreme conditions
- Safety: Enhanced containment structures and improved emergency response procedures
Outcome: Strengthened nuclear safety regulations globally, leading to more resilient and safer nuclear power plants.
Autonomous Vehicle Development
Industry: Automotive RAMS Application: Waymo Self-Driving Technology
Waymo’s self-driving technology demonstrates the critical role of RAMS in emerging technologies.
Key RAMS elements:
- Reliability: Redundant sensors and processing units
- Availability: Real-time data processing and decision-making capabilities
- Maintainability: Over-the-air software updates and modular hardware design
- Safety: Advanced collision avoidance systems and ethical decision-making algorithms
Outcome: Millions of miles driven with a strong safety record, paving the way for widespread adoption of autonomous vehicles.
Medical Imaging Equipment
Industry: Healthcare RAMS Application: Philips Azurion Image-Guided Therapy System
This advanced medical imaging system showcases RAMS integration in critical healthcare applications.
Key RAMS elements:
- Reliability: High-quality components and stringent quality control processes
- Availability: Rapid boot-up times and minimal downtime between procedures
- Maintainability: Remote diagnostics and easy-access design for quick repairs
- Safety: Radiation dose management features and fail-safe mechanisms
Outcome: Improved patient outcomes, reduced procedure times, and enhanced diagnostic accuracy.
Offshore Oil and Gas Platforms
Industry: Energy RAMS Application: Norwegian Continental Shelf Operations
Norway’s approach to offshore oil and gas operations demonstrates comprehensive RAMS integration in a challenging environment.
Key RAMS elements:
- Reliability: Corrosion-resistant materials and robust design for harsh marine conditions
- Availability: Redundant systems for critical operations and weather-resistant designs
- Maintainability: Modular construction allowing for easier repairs and upgrades
- Safety: Advanced fire suppression systems and emergency evacuation procedures
Outcome: Improved safety records, reduced environmental incidents, and increased operational efficiency in North Sea oil and gas production.
These examples illustrate how RAMS principles can be effectively integrated across various industries to enhance system performance, safety, and efficiency. They demonstrate that successful RAMS implementation often requires:
- A holistic approach considering all RAMS elements
- Adaptation to industry-specific challenges and regulations
- Continuous improvement based on operational data and incident analysis
- Investment in advanced technologies and innovative design approaches
By studying these real-world applications, engineers and system designers can gain valuable insights into effective RAMS integration strategies and their potential benefits across different engineering disciplines.
Recommended Future Learn Short CoursesBest Practices for RAMS Integration in Systems Engineering
Effective integration of Reliability, Availability, Maintainability, and Safety (RAMS) principles into systems engineering requires a structured approach. The following best practices can help organizations maximize the benefits of RAMS integration across various aspects of system development and management.
Early Integration and Comprehensive Modeling
Incorporating RAMS considerations from the earliest stages of system conceptualization is crucial. This early integration reduces costly redesigns and ensures that RAMS is inherent in the system architecture. Engineers should conduct preliminary RAMS analyses during the concept development phase and include RAMS specialists in initial design team meetings.
Alongside early integration, developing detailed models that capture the entire system’s behavior, including RAMS aspects, is essential. Tools like Reliability Block Diagrams (RBDs) and Fault Tree Analysis (FTA) can provide a clear understanding of system interdependencies and help identify critical components. These models should be regularly updated as the design evolves, ensuring they remain accurate representations of the system.
Data-Driven Approach and Continuous Monitoring
Basing RAMS analyses and decisions on robust, relevant data is fundamental to success. Organizations should establish comprehensive data collection systems and utilize historical data from similar systems when available. Implementing a Failure Reporting, Analysis, and Corrective Action System (FRACAS) can significantly enhance the accuracy of RAMS predictions and support continuous improvement efforts.
Continuous monitoring goes hand-in-hand with a data-driven approach. Implementing systems for ongoing RAMS performance monitoring allows for timely interventions and supports adaptive management strategies. Establishing key performance indicators (KPIs) for RAMS and conducting regular audits and reviews ensures sustained RAMS performance over time.
Cross-Functional Collaboration and Stakeholder Engagement
RAMS integration is not solely the responsibility of specialists; it requires collaboration across various engineering disciplines. Regular cross-functional team meetings and providing RAMS training to non-specialist team members can foster this collaboration. Encouraging open communication channels between departments ensures RAMS considerations are integrated across all aspects of system design and operation.
Equally important is the involvement of all relevant stakeholders in the RAMS integration process. Conducting stakeholder analysis to identify all relevant parties and holding regular meetings to gather input and share RAMS insights can lead to more comprehensive solutions. Tailoring RAMS communication to different stakeholder groups improves buy-in and captures valuable insights from various perspectives.
Lifecycle Perspective and Risk-Based Approach
Considering RAMS implications throughout the entire system lifecycle is crucial for long-term success. Developing lifecycle RAMS plans, from design through to decommissioning, helps optimize long-term system performance and reduces total ownership costs. Planning for system upgrades and component obsolescence as part of this lifecycle approach improves system sustainability.
A risk-based approach to RAMS integration ensures that resources are allocated efficiently. Conducting comprehensive system risk analyses and focusing efforts on high-risk areas allows organizations to address critical issues effectively. Developing risk mitigation strategies as part of RAMS planning provides a structured approach to managing potential problems before they arise.
Documentation and Advanced Technologies
Maintaining comprehensive documentation of RAMS analyses, decisions, and outcomes is vital for knowledge transfer and regulatory compliance. Establishing a centralized RAMS knowledge repository and implementing version control for RAMS documentation facilitates future improvements and aids in demonstrating compliance with industry standards.
Finally, leveraging advanced technologies can significantly enhance RAMS capabilities. Exploring AI and machine learning for predictive maintenance, implementing digital twin technology for real-time system monitoring, and utilizing big data analytics for comprehensive RAMS trend analysis can lead to more sophisticated and effective RAMS management.
By adhering to these best practices, organizations can effectively integrate RAMS principles into their systems engineering processes, leading to more reliable, available, maintainable, and safe systems. This integration ultimately results in improved performance, reduced lifecycle costs, and enhanced user satisfaction.
Making Informed Decisions
In the design and upkeep of technical systems, assessing risk levels and potential failure impacts is critical. By integrating system safety considerations into the wider RAMS framework, engineers can optimize system performance while protecting human life, the environment, and system assets.
For sound decision-making, engineers need to perform comprehensive risk evaluations, identify hazards, and analyze failure modes. This process reveals crucial failure modes that could cause safety hazards and offers insights into possible preventative measures. Compliance with pertinent safety standards and guidelines, such as MIL-STD-882, guarantees a methodical approach to hazard elimination and risk reduction.
Key aspects of informed decision-making in RAMS integration include:
- Comprehensive Risk Assessment: Utilize tools like Failure Mode and Effects Analysis (FMEA) and Fault Tree Analysis (FTA) to identify potential risks and their impacts.
- Hazard Identification: Systematically identify all potential hazards associated with the system throughout its lifecycle.
- Failure Mode Analysis: Understand how different components or subsystems might fail and the consequences of these failures.
- Preventative Measures: Develop and implement measures to prevent or mitigate identified risks and hazards.
- Standards Compliance: Adhere to relevant industry standards and guidelines to ensure a structured approach to safety and risk management.
- Iterative Process: Continuously reassess and update risk evaluations as the system design evolves or new information becomes available.
- Trade-off Analysis: Balance performance requirements with safety considerations, making informed decisions about acceptable levels of risk.
- Documentation: Maintain detailed records of all risk assessments, decisions made, and rationale behind those decisions for future reference and continuous improvement.
By following this structured approach to decision-making, engineers can create systems that not only meet performance requirements but also prioritize safety and reliability throughout the system’s lifecycle.
This section fits well before the Conclusion, as it emphasizes the practical application of RAMS principles in real-world engineering decisions. It also reinforces the importance of safety integration within the broader RAMS framework.
Conclusion
The integration of Reliability, Availability, Maintainability, and Safety (RAMS) into systems engineering is not just a technical necessity but a strategic imperative in today’s complex and interconnected world. Throughout this comprehensive guide, we have explored the multifaceted aspects of RAMS, from its fundamental principles to real-world applications across various industries.
Key takeaways from our exploration of RAMS integration include:
- Holistic Approach: RAMS is most effective when considered as an integrated whole rather than as separate components. The synergies between reliability, availability, maintainability, and safety create robust systems that can withstand challenges and perform optimally over their lifecycle.
- Early Integration: Incorporating RAMS principles from the earliest stages of system design yields the greatest benefits. This proactive approach minimizes costly redesigns and ensures that RAMS considerations are inherent in the system architecture.
- Industry-Specific Adaptations: While RAMS principles are universal, their application must be tailored to the specific needs and challenges of each industry. From healthcare to aerospace, each sector requires a unique balance of RAMS elements to achieve optimal outcomes.
- Safety Prioritization: In critical scenarios, safety must take precedence. However, this prioritization should not come at the expense of overall system performance. Striking the right balance is key to creating systems that are both safe and efficient.
- Data-Driven Decision Making: The effectiveness of RAMS integration relies heavily on robust data collection, analysis, and interpretation. Embracing a data-driven approach enables more accurate predictions, better decision-making, and continuous improvement.
- Continuous Improvement: RAMS is not a one-time implementation but an ongoing process. Regular monitoring, analysis, and adaptation are essential to maintain and enhance system performance over time.
- Cross-Functional Collaboration: Successful RAMS integration requires cooperation across various engineering disciplines and stakeholders. This collaborative approach ensures comprehensive consideration of all system aspects.
- Lifecycle Perspective: Considering RAMS throughout the entire system lifecycle, from conception to decommissioning, optimizes long-term performance and reduces total ownership costs.
- Technological Leverage: Emerging technologies like AI, IoT, and digital twins offer new opportunities to enhance RAMS capabilities, enabling more sophisticated analysis and real-time optimization.
- Cultural Integration: Beyond technical implementation, fostering a culture that values and prioritizes RAMS principles is crucial for long-term success.
As systems become increasingly complex and interdependent, the importance of RAMS in systems engineering will only grow. Organizations that effectively integrate RAMS principles will be better positioned to create systems that are not only reliable and safe but also adaptable to future challenges and opportunities.
The journey of RAMS integration is ongoing, requiring continuous learning, adaptation, and innovation. By embracing the principles and practices outlined in this guide, engineers and organizations can create systems that stand the test of time, perform optimally under various conditions, and prioritize the safety of users and the environment.
In an era where system failures can have far-reaching consequences, RAMS integration is not just about engineering excellence—it’s about responsible innovation and sustainable progress. As we look to the future, the principles of RAMS will undoubtedly play a crucial role in shaping the next generation of engineering marvels and in addressing global challenges across all sectors of industry and society.
Further Reading
For those interested in expanding their knowledge of RAMS principles and applications, the following books by respected authors in the field are recommended:
- “Practical Reliability Engineering” by Patrick D. T. O’Connor and Andre Kleyner This comprehensive text covers all aspects of reliability engineering and is widely regarded as a standard in the field.
- “Reliability, Maintainability and Risk: Practical Methods for Engineers” by David J. Smith Smith’s book provides practical guidance on the application of reliability and maintainability techniques in engineering.
- “System Reliability Theory: Models, Statistical Methods, and Applications” by Marvin Rausand and Arnljot Høyland This book offers a deep dive into the theoretical foundations of reliability engineering with practical applications.
- “Maintainability: A Key to Effective Serviceability and Maintenance Management” by Benjamin S. Blanchard, Dinesh Verma, and Elmer L. Peterson Focusing on maintainability, this book provides strategies for improving system serviceability and maintenance.
- “Safety-Critical Systems: Problems, Process and Practice” edited by Chris Dale and Tom Anderson This collection of papers offers insights into safety-critical systems across various industries.
- “Reliability Engineering and Risk Analysis: A Practical Guide” by Mohammad Modarres, Mark P. Kaminskiy, and Vasiliy Krivtsov A practical guide that combines theory with real-world applications of reliability engineering and risk analysis.
- “The RAMS Management Guideline” by Gian Paolo Barabino and Francesca Marotta This guideline provides a structured approach to implementing RAMS management in organizations.
- “Human Reliability Analysis: Context and Control” by Erik Hollnagel Hollnagel’s book focuses on the human factors aspect of reliability, which is crucial in many RAMS applications.
These books offer a mix of theoretical foundations and practical applications, covering various aspects of RAMS. They can provide valuable insights for both newcomers to the field and experienced professionals looking to deepen their understanding of RAMS principles and practices.
Comment on “The Integration of RAMS and Safety in Systems Engineering: A Comprehensive Guide”