If you’re delving into the world of safety systems across various industries, you’ve likely come across the terms Safety Integrity Level (SIL) and Failure Modes, Effects, and Diagnostic Analysis (FMEDA). These aren’t just industry jargon; they’re critical in evaluating the reliability and performance of safety systems. So, let’s roll up our sleeves and dive into the nitty-gritty of SIL and FMEDA in this comprehensive guide.
Table of Contents
- Understanding Safety Integrity Level (SIL)
- The Importance of SIL
- The Process of Calculating SIL
- What are the SIL Levels?
- The Role of FMEDA in the SIL Journey
- The Importance of FMEDA in SIL Assessment
- The Challenges in the SIL Journey
- Principal Obstacles for System Engineers
- Buncefield Oil Storage Depot in the United Kingdom in 2005 Case Study
- SIL Wrap Up
Understanding Safety Integrity Level (SIL)
Picture SIL as a reliable scale, ranging from 1 to 4, that measures the effectiveness of a safety function or system in reducing risks. When SIL 4 pops up on the scale, you’re looking at the highest level of risk reduction. This handy measure also indicates the probability of a safety function failing when it’s most needed, known as the probability of failure on demand (PFD).
The Importance of SIL
SIL isn’t just a number; it’s a vital tool in assessing how well safety functions and systems can prevent hazardous incidents and mitigate risks. It’s like a safety roadmap, guiding engineers to calculate the required SIL level for a specific safety function.
The Process of Calculating SIL
Calculating SIL is a multi-step journey that starts with identifying the safety function and conducting a thorough risk assessment. Based on this assessment, engineers define the required risk reduction. The journey continues as they analyse potential failure modes, calculate the PFD, and finally, assign the appropriate SIL level.
What are the SIL Levels?
Safety Integrity Level (SIL) is a relative level of risk-reduction provided by a safety function, or to specify a target level of risk reduction. In essence, it is a measurement of performance required for a safety instrumented function (SIF). The higher the SIL level, the lower the probability of failure on demand for the safety system and the better the system performance.
SIL levels are determined during the Risk Assessment process, which accounts for the likelihood and potential impact of an identified hazard. The levels are defined from SIL 1 to SIL 4, where SIL 1 represents the lowest level of safety protection and SIL 4 the highest.
Here’s what each SIL level generally represents
- SIL 1 – This level applies to the lowest safety functions, which typically do not require highly complex safety systems. The risk reduction associated with SIL 1 is generally modest, and it is often economically feasible to achieve SIL 1 with single safety barriers or less sophisticated systems.
- SIL 2 – SIL 2 is a moderate level of safety integrity, requiring more stringent control systems and safety barriers than SIL 1. It is common in industries where there is a considerable hazard if safety-related systems fail, but the complete mitigation of the risk can still be economical.
- SIL 3 – This level demands more rigorous safety requirements and involves the use of highly reliable hardware and sophisticated fault tolerances. SIL 3 is usually associated with high-risk industries such as oil and gas extraction, where the consequences of failure can be catastrophic.
- SIL 4 – SIL 4 is the highest level of safety integrity, associated with the most critical systems where risk must be minimized as much as possible. Achieving SIL 4 involves complex and often expensive safety system configurations. The probability of failure must be extremely low. Because of the high costs and engineering complexities involved, SIL 4 is rare in most industries.
The determination of the appropriate SIL for a given application involves a systematic process typically facilitated by risk assessment methodologies such as Fault Tree Analysis or Failure Mode and Effects Analysis. The chosen SIL level dictates the requirements for system design, components, and functionalities to ensure adequate safety performance. In many standards, the specific requirements that must be met in system architecture, redundancy, diagnostics, and testing increase with higher SIL levels.
The Role of FMEDA in the SIL Journey
FMEDA is another key player in this journey. It’s a technique used to evaluate the safety and reliability of a system by analysing its potential failure modes, their effects, and the system’s diagnostic capabilities. It’s like a detective, helping to uncover potential issues that could impact the safety function.
The Importance of FMEDA in SIL Assessment
FMEDA is a crucial part of the SIL assessment process. It helps identify potential failure modes and assess their impact on the safety function. It’s like a magnifying glass, providing valuable insights into the system’s diagnostic capabilities, including the effectiveness of built-in diagnostic features and the probability of false alarms or missed failures.
Aspect | Role in SIL Assessment | Benefits |
---|---|---|
Identification of Failure Modes | FMEDA identifies all conceivable failure modes of a system’s components. | Enhances the accuracy of risk assessments by providing detailed failure mode insights. |
Effects Analysis | Analyzes the effects of each failure mode on the overall system operation. | Helps in prioritizing risk mitigation strategies based on the impact of potential failures. |
Diagnostic Coverage | Assesses the effectiveness of diagnostic functions in detecting failures. | Improves system reliability by increasing the likelihood of early failure detection. |
Quantitative Data | Provides quantitative data on failure probabilities and their impacts. | Supports quantitative risk analysis and the setting of appropriate SIL levels. |
The Challenges in the SIL Journey
Like any journey, assessing and determining the Safety Integrity Level (SIL) of a system comes with its own set of challenges. From conducting accurate risk assessments to ensuring compliance with standards, system engineers need to navigate these challenges effectively to ensure the safety and reliability of their systems.
Principal Obstacles for System Engineers
Identifying and establishing the Safety Integrity Level (SIL) of a system presents a unique set of obstacles for system engineers. Keep the following difficulties in mind when carrying out SIL assessments on your forthcoming project:
- Thorough Risk Evaluation: Undertaking a complete and precise risk evaluation is vital to ascertain the necessary SIL level. Accumulating dependable data, contemplating various failure scenarios, and assessing the repercussions of potential failures are crucial elements of this procedure.
- Availability of Dependability Data: Having access to accurate and current reliability data for components and systems is a frequent obstacle. System engineers might have to depend on historical data, reliability databases, expert opinion, or carry out additional testing to acquire the necessary information.
- Intricacy and Interconnections: Contemporary systems are increasingly intricate, with numerous interconnections between components and subsystems. Assessing the impact of these interconnections and guaranteeing the overall system reliability can be a complex task.
- Upkeep and Diagnostics: Appropriate upkeep and diagnostics are crucial for achieving and sustaining the desired SIL. System engineers need to consider factors such as test intervals, maintenance procedures, and the efficacy of diagnostics in identifying failures.
- Adherence to Standards: Compliance with relevant industry standards and regulations is crucial for SIL assessments. Keeping up-to-date with the latest standards, comprehending their requirements, and ensuring adherence can be a taxing task.
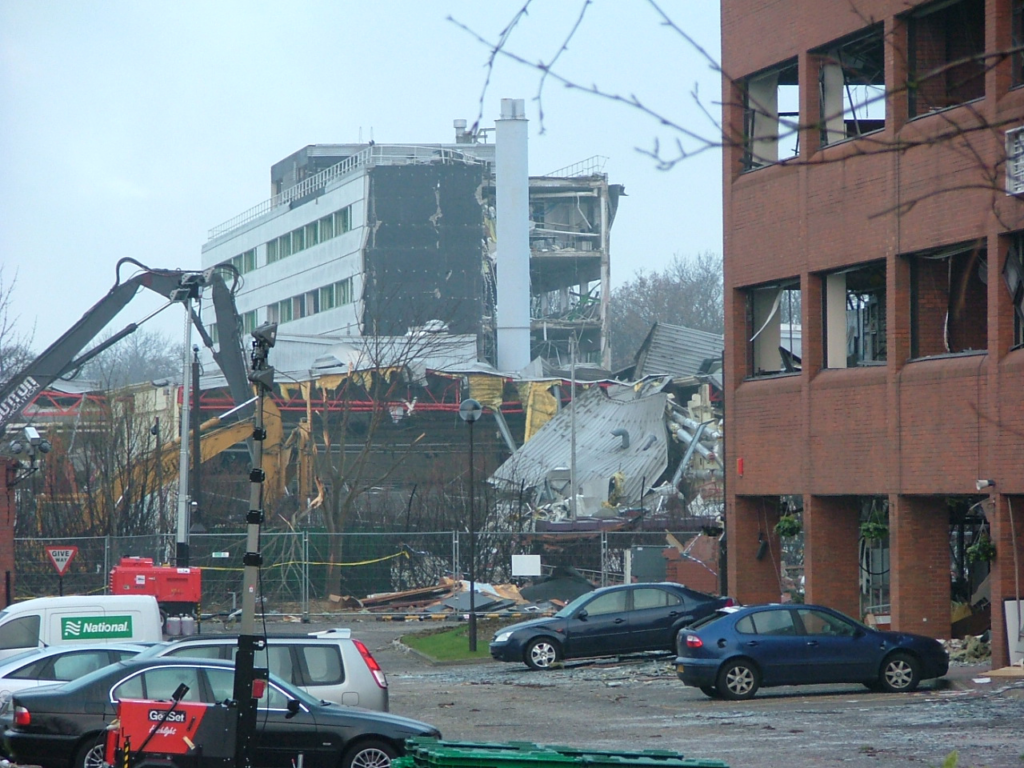
Buncefield Oil Storage Depot in the United Kingdom in 2005 Case Study
System engineers can promote accuracy and effectiveness in SIL assessments by tackling challenges. This leads to improved safety and reliability of systems.
One notable case study that underscores the importance of Safety Integrity Level (SIL) and the effectiveness of implementing robust safety systems is the incident at the Buncefield Oil Storage Depot in the United Kingdom in 2005.
Background
The Buncefield Oil Storage and Transfer Depot, located north of London, was one of the largest facilities of its kind in the UK. It played a critical role in distributing fuel around the country.
Incident Overview
On December 11, 2005, a series of explosions occurred at the depot, registering as a 2.4 magnitude earthquake on seismic devices. This catastrophic event was primarily caused by the overflow of gasoline from one of the storage tanks. A major factor leading to the overflow was the failure of the tank’s automatic tank gauging system, which should have alerted operators to the high level of fuel. The vapors from the overflowed petrol formed a large vapor cloud, which ignited and resulted in large-scale explosions and fires.
Safety and SIL Considerations
Pre-incident, the facility relied on level sensors and associated safety alarms to prevent such overflows. However, investigations revealed several failures in safety system management, including the level monitoring systems not being certified to any SIL level. The absence of functional safety assessments and inadequate SIL implementation for critical safety systems led to a lack of sufficient risk management measures.
Consequences
The explosions injured 43 people, and the ensuing fires caused extensive property damage—not only within the facility but also in surrounding areas. Economically, the incident was devastating, impacting businesses and the overall fuel supply chain in the UK. It highlighted significant shortcomings in safety standards and risk assessments at critical facilities.
Lessons Learned and SIL Implications
Post-incident analysis stressed the need for rigorous adherence to safety standards, including the implementation of SIL-rated systems for critical safety functions. The incident spurred re-evaluations of existing safety procedures and reinforced the importance of SIL assessments in identifying and mitigating risks.
This case study is often referenced in discussions about industrial safety regulations and is used as a benchmark for improving safety measures in similar facilities worldwide. The Buncefield incident illustrates the disastrous consequences of failing to properly implement and maintain SIL standards, underscoring the critical role of safety systems in industrial operations.
SIL Wrap Up
Safety Integrity Level (SIL) and Failure Modes, Effects, and Diagnostic Analysis (FMEDA) play a vital role in maintaining system reliability. With a clear understanding and approach towards these challenges, improved SIL assessment is achievable. This results in heightened system safety and dependability. Whether you are an experienced engineer or a novice, mastering SIL and FMEDA is a worthwhile skill set.