In the dynamic field of project management, successful project delivery does not mark the end but rather a transition to continuous stewardship. Upon completing a construction project, it must be handed over to the operator and maintainer who will assume responsibility for its ongoing operation. While risk transfer plays a vital role in mitigating risks during the design and construction phases, it is crucial to recognize that risks still exist even after project completion. This in-depth article explores the importance of comprehensive risk management during project handover, shedding light on the transfer of risks from the construction phase to the operational phase. Join us as we unravel the intricacies of safeguarding construction investments and ensuring long-term success.
Table of Contents
The Handover Process: From Construction to Operation
The handover process is a critical juncture in the lifecycle of any project, marking the transition from construction to operation. This stage is not only about declaring the physical completion of the asset but also about ensuring that it is fully prepared for operational demands. The focus here is on transferring responsibility from the construction team to the operators and maintainers, who will oversee its day-to-day functionality.
Key Components of the Handover Process
- Operational Readiness Assessment: Before the handover, it is vital to ensure that the project is operationally ready. This involves rigorous testing of systems, equipment, and infrastructure to ensure they meet the designed performance criteria and safety standards.
- Detailed Documentation: Comprehensive documentation is essential for an effective handover. This includes as-built drawings, equipment manuals, maintenance schedules, and safety protocols. Proper documentation equips the operational team with the knowledge required to manage the asset efficiently.
- Training and Support: Providing targeted training sessions is crucial to prepare the operational team for their new responsibilities. This training should cover the operation of new equipment, maintenance procedures, safety measures, and emergency response plans.
- Stakeholder Communication: Effective communication between all involved parties ensures that everyone is informed about the status and expectations of the handover. Regular meetings and updates can help align the contractor, operator, and maintainer on the condition and operational readiness of the handed-over asset.
Industries Impacted by the Handover Process
The need for a well-structured handover process is particularly evident in industries where the seamless transition from construction to operation is critical for safety, efficiency, and long-term success. This includes but is not limited to:
- Construction and Infrastructure: Projects such as bridges, highways, and buildings, where operational readiness includes ensuring structural integrity and compliance with safety standards.
- Energy Sector: In power plants, oil and gas refineries, and renewable energy installations, the transition to operational maintenance is complex and requires meticulous planning and risk assessment.
- Manufacturing: Factories and production facilities where the smooth startup of operational processes is crucial for maintaining productivity and safety.
- Healthcare: Hospitals and medical facilities, where operational readiness directly impacts patient care and safety.
- Transportation: Airport terminals, railways, and seaports, where operational readiness ensures the smooth functioning of transport systems and the safety of passengers.
Ensuring a Smooth Transition
A well-planned and executed handover process mitigates the risks associated with transitioning to the operational phase. Here are some steps to ensure a smooth transition:
- Pre-Handover Risk Assessment: Conduct a thorough risk assessment to identify any lingering issues that need to be addressed before the handover.
- Handover Meetings: Organize regular handover meetings between the project team and the operational team to address any concerns and ensure that all information is adequately communicated.
- Punch List Management: Develop and manage a punch list of items that need to be corrected or completed before the final handover. Keep it updated and ensure that each task is resolved timely.
By focusing on these key components, project teams can ensure that the transition from construction to operation is as smooth and risk-free as possible. This structured approach helps mitigate potential risks, align all stakeholders, and set a solid foundation for the long-term success and sustainability of the project.
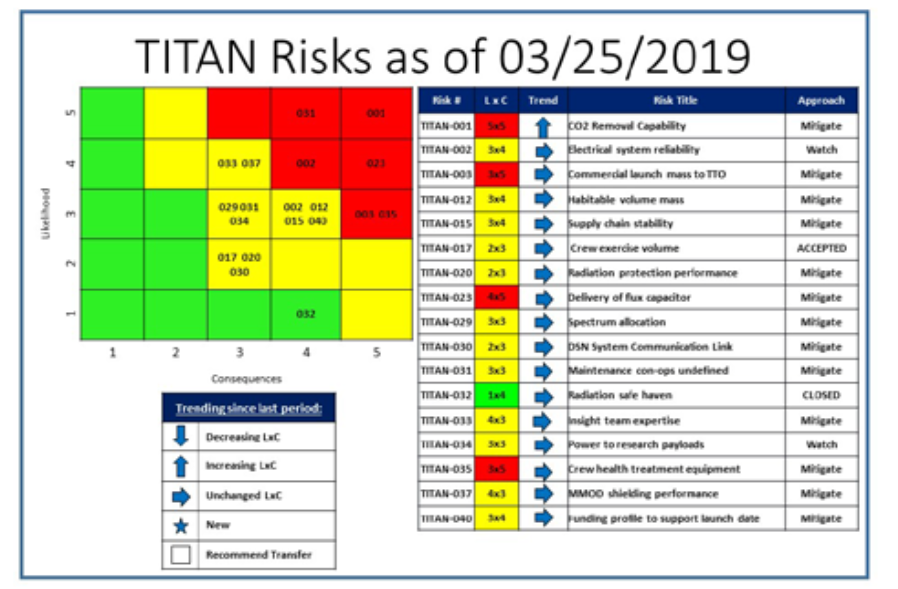
What is Residual Risk?
Residual risk is the term used to describe the risk that remains after all planned risk management measures, such as risk transfer, mitigation strategies, and safety protocols, have been implemented. In simpler terms, it is the risk that persists even after you have taken steps to eliminate or reduce the impact of potential hazards.
Characteristic | Description |
---|---|
Inevitable | Despite extensive risk management efforts, some level of risk will always remain. This inevitability stems from inherent uncertainties, unknown variables, and the limitations of risk control measures. Every project, regardless of its thorough planning and execution, faces unknowns that can’t be fully mitigated. As such, residual risk is a fundamental aspect of all project undertakings. |
Managed | Residual risks are acknowledged and managed through continuous monitoring and adaptive strategies. This involves recognizing that some risks remain post-mitigation and proactively managing these risks by regular tracking and assessing risk levels to detect any changes or new emerging risks, adjusting and updating risk management plans based on real-time data and evolving project dynamics, and ensuring that all team members are aware of potential residual risks and are trained to handle them effectively. |
Quantified | Residual risks are often quantified in terms of their likelihood and impact, helping prioritize further actions. Quantification provides a structured approach to understanding and managing these risks. This involves determining the probability of residual risks occurring based on historical data and expert judgment, evaluating the potential consequences of these risks on project objectives, timelines, and resources, and using tools such as risk matrices or scoring systems to categorize and prioritize risks based on their quantification. |
Example in Construction Projects
In the context of construction projects, consider a scenario where you have identified the risk of equipment failure. You may:
- Implement a regular maintenance schedule (mitigation)
- Train staff on proper equipment use (training)
- Include clauses in contracts to hold suppliers accountable for substandard equipment (risk transfer)
Despite these efforts, there remains a small possibility that equipment could still fail due to unforeseen reasons. This small possibility is the residual risk.
Identifying and Transferring Risks in Construction Projects
In the realm of project management, risk identification and transfer are crucial elements that ensure the successful delivery and ongoing safe operation of assets. During the design and construction phases, a structured approach to risk management helps allocate specific risks to the appropriate parties, thereby mitigating potential negative impacts on the project. This section delves into the principles and practices of risk transfer and the importance of systems integration and systems engineering in maintaining safe operations.
Risk Transfer: A Key Element in Project Delivery
Risk transfer is a strategic method used to allocate specific risks to contractors, suppliers, and other stakeholders through contractual agreements. This approach aims to manage the uncertainties inherent in complex projects and to ensure that those best equipped to handle specific risks are responsible for doing so.
- Contractual Agreements: Comprehensive contracts clearly delineate the responsibilities and liabilities of each party involved in the project. By specifying who is responsible for which risks, these agreements can significantly reduce the likelihood of disputes and project delays.
- Insurance Policies: Various insurance policies, including builders’ risk insurance and professional liability insurance, provide additional layers of protection, ensuring that financial losses due to unforeseen events are minimized.
- Performance Bonds: These bonds guarantee that contractors will fulfill their contractual obligations or compensate the project owner accordingly, offering an added level of security.
Risks Transferred During Construction
During the construction phase, numerous risks are transferred from the project owner to the contractors and suppliers. These risks can encompass a variety of issues:
- Delays: Time-related risks due to scheduling errors, contractor inefficiencies, or external factors like weather conditions.
- Material Shortages: Risks associated with the unavailability or delayed delivery of construction materials.
- Quality Control: Ensuring that the work meets the specified standards and adheres to industry regulations.
- Compliance: Adherence to local, state, and federal regulations, as well as obtaining the necessary permits and inspections.
Systems Integration and Systems Engineering Principles
To manage these risks effectively and ensure the safe operation of assets, project teams often rely on systems integration and systems engineering principles. These methodologies provide a holistic approach to managing complex projects by focusing on the integration of different systems and processes to achieve a seamless and well-coordinated outcome.
- Systems Integration: This involves the process of bringing together various subsystems into one unified system, ensuring they function effectively together. In construction projects, systems integration can include combining electrical, mechanical, structural, and IT systems to operate harmoniously. By addressing interoperability and compatibility issues early, project teams can minimize risks and enhance overall efficiency.
- Systems Engineering: Systems engineering principles offer a structured approach to designing, integrating, and managing complex systems over their life cycles. This discipline emphasizes the consideration of all aspects of a project, from initial requirements gathering to design, implementation, testing, and maintenance. Key aspects include:
- Risk Management: Identifying potential risks early and developing mitigation strategies.
- Requirements Analysis: Ensuring that all stakeholder requirements are captured and met.
- Verification and Validation: Testing systems using verification and validation techniques to ensure they operate correctly and meet all requirements.
- Lifecycle Management: Planning for long-term maintenance and updates to the system.
Implementing Risk Transfer Through Systems Engineering
By leveraging systems engineering principles, project teams can effectively manage and transfer risks during construction. This approach not only ensures that risks are allocated to the appropriate parties but also promotes safe and efficient operations throughout the asset’s lifecycle.
- Comprehensive Risk Assessments: Conducting detailed risk assessments that consider both individual subsystems and the integrated whole.
- Iterative Design and Testing: Using iterative cycles of design, testing, and refinement to identify and mitigate risks early.
- Robust Documentation: Maintaining thorough documentation that captures all aspects of design, implementation, and operational protocols, aiding in future maintenance and troubleshooting efforts.
By employing these principles, project teams can ensure that risks associated with construction projects are effectively managed and transferred, resulting in the safe and sustainable operation of the completed asset.
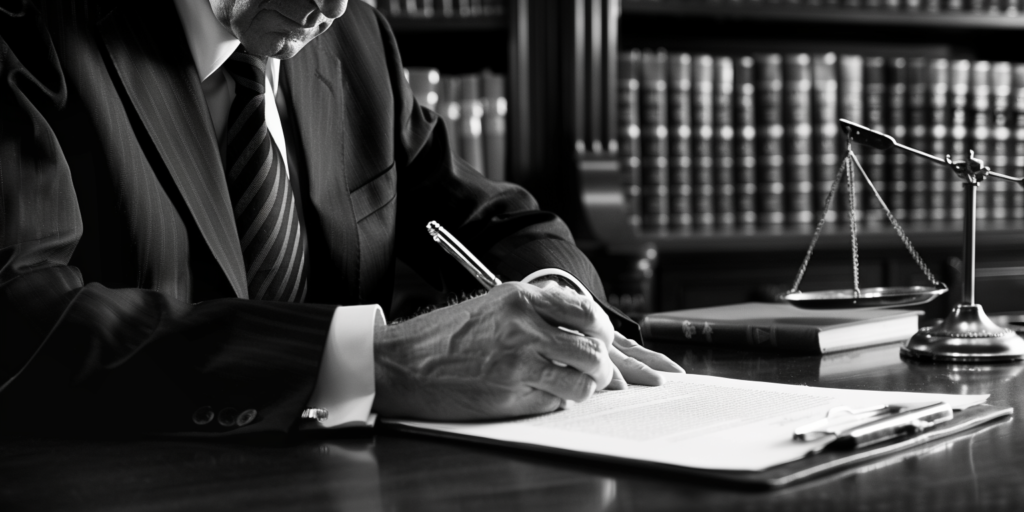
Understanding Post-Construction Risks
When a construction project transitions from the construction phase to the operational phase, the nature of the risks changes significantly. While some risks are effectively transferred and managed during construction, new risks emerge that require careful attention to ensure the long-term success and safety of the asset. Understanding these post-construction risks and implementing proactive mitigation strategies is crucial for safeguarding the investment.
Risks in the Operational Phase: A Shift in Focus
Once a project is handed over for operation, the focus shifts from construction-related risks to those associated with day-to-day operations. Operational risks encompass a wide range of issues, from equipment malfunctions to regulatory compliance. Recognizing and addressing these risks early on is vital for maintaining continuous, safe, and efficient operations.
- Equipment Maintenance: Comprehensive maintenance plans are essential to ensure that all equipment operates within designed parameters, minimizing the risk of unexpected failures.
- System Breakdowns: Regularly scheduled inspections and timely repairs are critical to preventing system breakdowns that could disrupt operations.
- Environmental Impact: Monitoring environmental conditions and implementing measures to mitigate any negative impact are necessary for compliance with environmental regulations.
- Regulatory Compliance: Adapting to and complying with evolving regulations helps avoid legal issues and potential fines.
- Occupational Health and Safety: Ensuring a safe working environment reduces the risk of accidents and promotes worker well-being.
Identifying Post-Construction Risks
To effectively manage post-construction risks, a comprehensive risk assessment is required. This assessment should consider various factors, including equipment reliability, maintenance requirements, environmental impacts, and regulatory changes. Below is a table outlining common post-construction risks and key mitigation strategies to address each.
Risk Category | Description | Key Mitigation Strategies |
---|---|---|
Equipment Maintenance | Potential failure of critical equipment due to wear and tear. | – Implement preventive and predictive maintenance schedules – Conduct regular inspections and diagnostics – Use condition monitoring technologies |
System Breakdowns | Disruptions due to malfunctions in integrated systems. | – Establish redundant systems and backup plans – Conduct regular system audits and simulations – Train staff in rapid response and troubleshooting |
Environmental Impact | Negative effects on the environment from operational activities. | – Monitor and control emissions and waste – Implement environmentally friendly practices – Regularly review and update environmental management plans |
Regulatory Compliance | Non-compliance with evolving laws and regulations. | – Stay informed about regulatory changes and updates – Conduct regular compliance audits – Engage with legal advisors to ensure adherence |
Occupational Health and Safety | Risks to worker health and safety during operations. | – Implement stringent safety protocols and training programs – Conduct regular safety drills and audits – Provide necessary personal protective equipment (PPE) |
Cybersecurity Threats | Risks related to cyber-attacks and data breaches. | – Implement robust cybersecurity measures – Educate staff on security best practices – Regularly update software and security protocols |
Financial Risks | Unexpected operational costs and budget overruns. | – Develop detailed financial plans and contingencies – Monitor expenses regularly – Use financial management software for tracking and forecasting |
Supply Chain Disruptions | Delays and disruptions in the supply chain impacting operations. | – Develop strong relationships with multiple suppliers – Maintain a buffer stock of critical supplies – Use supply chain management tools to anticipate and mitigate risks |
Implementing Mitigation Strategies
Effective risk mitigation in the operational phase requires a proactive and systematic approach. Here are some steps to implement these strategies:
- Risk Assessment: Conduct regular risk assessments to identify and prioritize potential risks.
- Documentation and Procedures: Develop and maintain comprehensive documentation outlining procedures and protocols for addressing identified risks.
- Training and Education: Continuously train staff on the latest operational procedures, safety protocols, and risk mitigation practices.
- Collaboration and Communication: Foster open communication and collaboration among all stakeholders, including operators, maintainers, and regulatory bodies.
- Technological Advancements: Leverage new technologies and innovative solutions to monitor, detect, and mitigate risks effectively.
By understanding and addressing these post-construction risks, project teams can ensure that the asset operates safely, efficiently, and sustainably over its entire lifecycle. Implementing robust risk management practices will not only protect the investment but also contribute to the long-term success and resilience of the project.
Recommended Further Reading Amazon BooksThe Role of Safety Cases in Infrastructure Projects
Safety cases are essential documents in infrastructure projects, serving as comprehensive assessments that demonstrate a project’s safety to stakeholders, regulators, and the public. They play a critical role in ensuring that all safety aspects of a project are adequately considered and managed throughout its lifecycle.
What is a Safety Case?
A safety case is a structured argument, supported by evidence, that provides assurance that a system or operation is safe for a specific application within a defined context. It encompasses all elements of design, construction, operation, and maintenance, ensuring that safety is considered at every stage.
Key Components of a Safety Case
- System Description: Comprehensive details of the infrastructure system, including design specifications, operational context, and intended use.
- Hazard Identification and Risk Assessment: Systematic identification of potential hazards and a thorough risk assessment to understand their likelihood and impact.
- Safety Measures and Controls: Documentation of all safety measures, controls, and mitigation strategies implemented to address identified hazards.
- Safety Management System: Details of policies, procedures, and responsibilities that contribute to ongoing safety management.
- Evidence and Assurance: Collection of evidence, such as test results, simulations, audits, and inspections, that demonstrate the system’s safety and the efficacy of controls.
- Stakeholder Involvement and Communication: Processes for involving stakeholders in safety discussions, ensuring transparency, and addressing their concerns.
Ensuring Adequacy of Safety Cases
- Comprehensive Assessment: A safety case should comprehensively cover all potential hazards and risks. This includes understanding the interaction between various subsystems and considering worst-case scenarios.
- Iterative Reviews: Safety cases should be living documents, updated regularly to reflect changes in the project, new hazards, and improvements in safety measures.
- Third-Party Audits: Independent audits can provide an objective review of the safety case, ensuring all assumptions and mitigations are valid and effective.
Achieving Stakeholder Acceptance
- Engagement and Communication: Early and continuous engagement with stakeholders, including the public and regulatory bodies, is crucial. Transparent communication about risks, safety measures, and the rationale behind decisions fosters trust and acceptance.
- Demonstrating Due Diligence: Clearly demonstrating that all reasonable steps have been taken to ensure safety can help gain stakeholder confidence. This might include detailed risk assessments, robust safety controls, and adherence to industry best practices.
- Addressing Concerns: Proactively addressing stakeholder concerns and incorporating their feedback into the safety case helps in achieving broader acceptance. This might involve public consultations, information sessions, and ongoing dialogues.
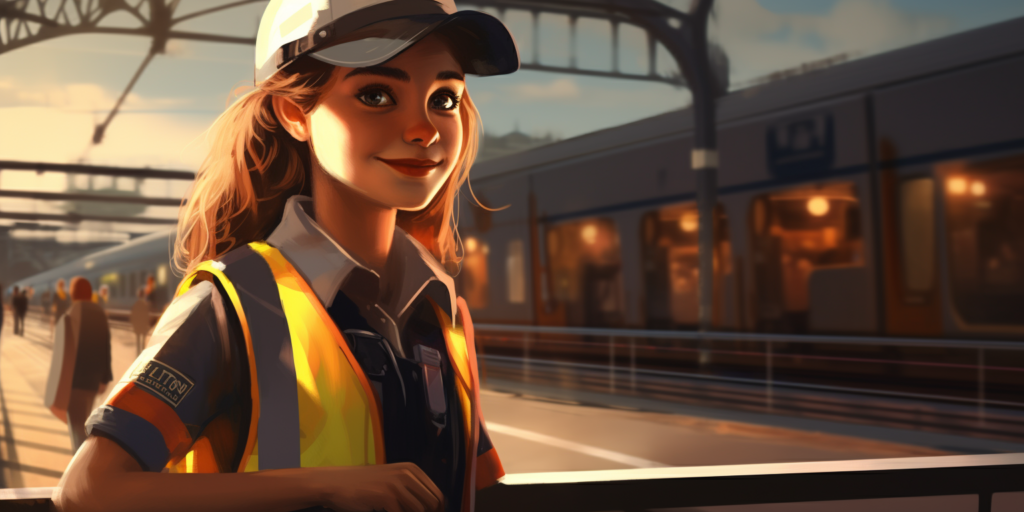
Example of Safety Case Application
Consider a major infrastructure project like a railway network expansion. The safety case for this project would detail the design of new tracks, signaling systems, and trains, identify potential hazards (e.g., derailments, signal failures), and describe how these risks are mitigated. It would also demonstrate compliance with all relevant safety regulations and standards, supported by evidence from simulations, pilot runs, and third-party audits.
By providing a structured and transparent rationale for safety, safety cases ensure that infrastructure projects are robustly assessed for safety and gain the necessary approvals and stakeholder acceptance, ultimately contributing to the project’s long-term success and sustainability.
Comprehensive Risk Management in Project Handover
Transitioning from the construction phase to the operational phase of a project requires not just a handover of the physical asset but also a thorough and ongoing risk management strategy. This section explores the essential components of a comprehensive risk management approach during project handover, which are critical to ensuring the project’s long-term success and sustainability.
Establishing Effective Communication and Collaboration
Effective communication and collaboration between the construction team, operator, and maintainer are fundamental for a seamless transition. Key practices include:
- Handover Meetings: Regularly scheduled meetings to discuss progress, share updates, and address concerns.
- Stakeholder Involvement: Ensuring all relevant stakeholders are involved in handover discussions to align expectations and responsibilities.
- Clear Reporting Channels: Establishing clear lines of communication to facilitate real-time problem-solving and decision-making.
Documentation and Knowledge Transfer
Thorough documentation and knowledge transfer are paramount to effective risk management during handover. These practices ensure that the operational team is well-equipped to manage the asset:
- As-Built Documentation: Comprehensive records of the as-built condition, including diagrams, schematics, and specifications.
- Operational Manuals: Detailed guides on operating, maintaining, and troubleshooting equipment and systems.
- Maintenance Logs: Records of maintenance schedules, procedures, and historical data to inform future upkeep.
Training and Skills Development
Adequate training and skills development are crucial for the operational team to mitigate post-construction risks. Focus areas include:
- Equipment Operation: Training on the safe and efficient use of all operational equipment.
- Maintenance Procedures: Educating staff on preventive and corrective maintenance practices.
- Safety Protocols: Regular safety training to ensure compliance with health and safety regulations.
- Emergency Response: Drills and training sessions to prepare staff for emergency scenarios.
Continuous Monitoring and Review
Ongoing risk management requires regular monitoring and periodic reviews to identify and address emerging risks:
- Performance Audits: Conducting regular audits to assess operational performance and identify potential improvements.
- Risk Assessments: Periodically updating risk assessments to reflect changes in the operational environment.
- Feedback Mechanisms: Implementing mechanisms for continuous feedback from the operational team to identify and rectify issues promptly.
Collaborative Problem-Solving
Fostering a culture of collaborative problem-solving is essential for addressing unforeseen challenges during the operational phase:
- Cross-Functional Teams: Integrating expertise from various disciplines to develop holistic solutions.
- Open Communication: Encouraging open discussion of issues to leverage diverse insights and experiences.
- Innovative Solutions: Promoting creativity and innovation in developing risk mitigation strategies.
Regular Maintenance and Inspections
Scheduled maintenance activities and routine inspections are critical to identifying and mitigating potential issues before they escalate:
- Preventive Maintenance: Implementing maintenance schedules based on manufacturer recommendations and industry best practices.
- Routine Inspections: Conducting frequent inspections to monitor equipment and system conditions.
- Predictive Analytics: Utilizing predictive maintenance technologies to anticipate and address potential failures.
Adapting to Regulatory Changes
Staying compliant with evolving regulatory frameworks is crucial to minimizing legal risks and ensuring safe operations:
- Regulatory Monitoring: Keeping abreast of changes in relevant regulations and standards.
- Compliance Audits: Regularly auditing operational practices to ensure ongoing compliance.
- Engagement with Regulators: Establishing relationships with regulatory bodies for guidance and updates on new requirements.
Monitoring Technological Advancements
In the rapidly evolving technological landscape, staying updated with emerging trends and advancements can significantly enhance risk management:
- Technology Implementation: Integrating advanced technologies such as IoT, AI, and machine learning for improved operational efficiency and risk mitigation.
- Continuous Learning: Encouraging ongoing education and training on new technologies and their applications.
- Innovation Watch: Regularly reviewing and considering the applicability of new technologies to the project.
By focusing on these comprehensive risk management strategies during the project handover, project teams can ensure that the asset is well-prepared for long-term, sustainable operations. This approach not only mitigates potential risks but also contributes to the overall success and resilience of the project.
Conclusion
Comprehensive risk management during the project handover phase is a critical determinant of a project’s long-term success and sustainability. While risk transfer methodologies during the design and construction phases play a significant role in mitigating potential issues, it is essential to understand that risks persist even after project completion. Through diligent identification and management of post-construction risks, fostering effective communication and collaboration, and deploying thorough documentation, training, and continuous monitoring strategies, project teams can ensure that the transition from construction to operation is smooth and effective.
Moreover, integrating systems engineering principles and staying adaptive to technological advancements and regulatory changes can further bolster the robustness of operational risk management. By embracing a holistic and proactive approach to risk management throughout the operational phase, project teams can safeguard construction investments, maintain operational efficiency, and uphold safety standards, thereby ensuring long-term project success and enhancing the reputation of all stakeholders involved.
References for Further Reading
For readers interested in delving deeper into the topics discussed in this article, the following references offer valuable insights and detailed information:
- Guide to the Project Management Body of Knowledge (PMBOK® Guide) – Project Management Institute (PMI)
- This comprehensive guide provides in-depth knowledge on project management principles and practices, including risk management methodologies.
- Systems Engineering Handbook: A Guide for System Life Cycle Processes and Activities – International Council on Systems Engineering (INCOSE)
- A pivotal resource for understanding systems engineering principles and their application to complex projects.
- Construction Project Management: A Practical Guide to Field Construction Management – S. Keoki Sears, Glenn A. Sears, Richard H. Clough, Jerald L. Rounds, Robert O. Segner
- This book offers practical insights into managing construction projects, including risk management and the handover process.
- Managing Risks in Construction Projects – Helen Lingard, Stephen Rowlinson
- An essential text focusing on risk management in construction, providing strategies and real-world examples.
- Maintenance and Reliability Best Practices – Ramesh Gulati
- A must-read for understanding maintenance strategies and reliability management to mitigate operational risks.
- Project Risk Management: Processes, Techniques, and Insights – Chris Chapman, Stephen Ward
- This book provides a detailed exploration of risk management processes and techniques applicable to project management.
- ISO 31000: Risk Management – Guidelines – International Organization for Standardization (ISO)
- ISO 31000 provides guidelines on risk management principles and implementation, applicable across various industries.
- Standards for Occupational Health and Safety – Occupational Safety and Health Administration (OSHA)
- OSHA’s standards and guidance documents offer invaluable information on maintaining workplace safety and compliance.