The journey from a conceptual vision to an operational system is paved with crucial steps, none more important than the translation of a Concept of Operations (CONOPS) into clear, actionable operational requirements. While CONOPS paints the picture of what a system should do and how it should operate, operational requirements provide the detailed specifications that make that vision achievable.
In today’s complex transportation systems, whether developing new infrastructure, modernizing existing assets, or integrating emerging technologies, the gap between concept and implementation must be bridged with precision and clarity. The process of defining operational requirements serves as this bridge, transforming high-level operational concepts into specific, measurable criteria that guide system development, testing, and acceptance.
Recent experiences in major transportation projects worldwide have demonstrated that poorly defined operational requirements can lead to significant challenges. These range from systems that fail to meet user needs to cost overruns and delayed implementations. For instance, several recent automated transit projects faced operational challenges not because of technical failures, but due to requirements that didn’t fully capture the operational complexity of real-world scenarios.
This article explores the systematic approach to developing operational requirements from an established CONOPS. Drawing from international best practices and lessons learned across various transportation sectors, we’ll examine how organizations can effectively translate operational concepts into clear, testable requirements that ensure successful system delivery.
Understanding this process is crucial for transportation professionals, systems engineers, project managers, and stakeholders involved in system development. Whether you’re working on rail systems, bus networks, traffic management systems, or multimodal transportation hubs, the principles and approaches discussed here will help ensure your operational requirements effectively support your system’s intended use.
Recommended Further Reading Amazon BooksTable of Contents
1. Foundations of Operational Requirements
Converting a CONOPS into actionable requirements demands a structured approach built on solid foundations. These foundations ensure requirements align with organizational objectives while remaining practical and achievable across different industries and applications.
Strategic Alignment
The first step in developing operational requirements is ensuring alignment with enterprise objectives. In defense projects, this might mean mapping requirements to military capability needs; in manufacturing, to production efficiency targets; and in transportation, to service delivery standards. For example, a defense communication system’s requirements must align with battlefield information sharing objectives, while a manufacturing plant’s automation requirements must support specific production throughput goals.
Performance Capability Metrics
Operational requirements must be anchored in measurable performance metrics. These vary significantly by industry:
- Transportation: Metrics might include passenger throughput, service frequency, or system availability
- Manufacturing: Production rate, quality tolerances, or equipment utilization rates
- Defense: Mission success rates, deployment times, or system reliability under stress
- Healthcare: Patient throughput, response times, or equipment availability
The key is establishing metrics that are both meaningful and measurable. For instance, a metro system might specify “99.5% service availability during peak hours,” while a manufacturing plant might require “production line changeover in less than 30 minutes.”
Service Level Framework
Operational requirements typically span three distinct levels:
- Strategic Level
- Long-term capability objectives
- System-wide performance targets
- Enterprise-level integration needs
- Tactical Level
- Medium-term operational targets
- Resource allocation requirements
- Interface specifications
- Operational Level
- Day-to-day functional requirements
- User interaction specifications
- Maintenance and support needs
For example, an air traffic control system’s strategic requirements might address long-term airspace capacity, while tactical requirements focus on controller workload management, and operational requirements specify real-time system response times.
Assumptions and Constraints
Every operational requirement exists within a framework of assumptions and constraints. These must be explicitly documented to ensure requirements remain realistic and achievable. Common categories include:
- Technical Constraints: Such as existing infrastructure limitations or technology compatibility requirements
- Regulatory Requirements: Including safety standards, environmental regulations, or industry-specific compliance needs
- Resource Limitations: Both human and material resources available for system operation
- Environmental Conditions: Operating environment constraints, from weather conditions to electromagnetic interference
In healthcare, for instance, requirements for a new patient monitoring system must consider existing hospital infrastructure, medical device regulations, staff availability, and 24/7 operational demands. Similarly, a military drone system must account for battlefield conditions, communication security requirements, and operator skill levels.
Dependencies
Modern systems rarely operate in isolation. Operational requirements must acknowledge and address various dependencies:
- Internal Dependencies: Between different system components or subsystems
- External Dependencies: With other systems, organizations, or infrastructure
- Temporal Dependencies: Related to timing, sequencing, or scheduling
- Resource Dependencies: Including personnel, equipment, or supplies
A manufacturing control system, for example, must interface with enterprise resource planning systems, quality control systems, and supply chain management systems, each with its own operational requirements and constraints.
By carefully considering these foundational elements, organizations can develop operational requirements that are both comprehensive and achievable. This structured approach ensures that requirements effectively bridge the gap between conceptual operations and practical implementation, regardless of the industry or application.
Recommended Further Reading Amazon Books2. Core Requirement Categories
The transformation of CONOPS into operational requirements demands careful categorization to ensure comprehensive coverage of all system aspects. While specific needs vary across industries, certain core categories are universal in their application.
The following table provides a structured overview of essential requirement categories, with examples from different sectors to illustrate their application:
Requirement Category | Description | Transportation Example | Defense Example | Manufacturing Example |
---|---|---|---|---|
Physical Systems | Requirements related to tangible assets and infrastructure | Train control system response time < 0.5 seconds | Aircraft sortie generation rate of 6 per day | Production line changeover < 30 minutes |
User Interface | How operators and users interact with the system | Control room displays visible from 3m in all lighting conditions | Wearable combat system operable with gloves | Machine controls accessible during operation while wearing PPE |
Performance | Quantifiable system outputs and capabilities | 99.5% service availability during peak hours | 95% probability of detection at 40km range | Production yield rate > 98% |
Environmental | Operating environment conditions and constraints | System operation in -20°C to +45°C | Desert operations in sandstorm conditions | Clean room particle count < 100 per cubic foot |
Reliability | System dependability and maintenance needs | Mean time between failures > 50,000 hours | Mission reliability > 98% | Unplanned downtime < 2% |
Security | Protection against threats and unauthorized access | Multi-factor authentication for critical controls | Encrypted communications with NSA standards | Cybersecurity compliance with ISO 27001 |
Safety | Protection of people and assets | Emergency stop activation < 2 seconds | Weapon safety interlocks with 100% reliability | Machine guarding with redundant sensors |
Integration | Interface with other systems and processes | Real-time data exchange with adjacent systems | Joint force interoperability standards | ERP system integration < 50ms latency |
Training | Operator and maintainer capability development | Operator certification within 40 hours | Combat readiness training within 12 weeks | Maintenance tech qualification in 5 days |
Documentation | Required system documentation and records | Electronic maintenance records retention 7 years | Mission data recording for 72 hours | Quality records maintained for 5 years |
Additional Considerations
Beyond these core categories, operational requirements must also address:
Scalability Requirements
- Future capacity expansion
- System growth capabilities
- Resource scaling needs
Transition Requirements
- Migration from existing systems
- Phased implementation approaches
- Temporary operational modes
Emergency Operations
- Degraded mode operations
- Backup systems and procedures
- Recovery processes
Each requirement category must be tailored to the specific industry context while maintaining clear traceability to the original CONOPS. The key is ensuring requirements are specific, measurable, achievable, relevant, and time-bound (SMART), regardless of the industry or application.
Recommended Future Learn Short Courses3. Development Process
Transforming CONOPS into operational requirements follows a systematic process that ensures completeness, accuracy, and stakeholder alignment. This process, while rigorous, must remain flexible enough to accommodate diverse project needs across industries.
Requirements Elicitation
Requirements elicitation begins with structured analysis of the CONOPS document, focusing on:
- Operational scenarios
- User needs and expectations
- Performance parameters
- System interfaces
Key activities include:
- Stakeholder workshops
- Scenario analysis
- Interface mapping
- Performance modeling
Documentation Framework
Requirements must be documented in a clear, traceable format:
Requirement ID: OPS-001
Category: Performance
Description: The system shall process incoming data within [X] seconds
Verification: System test under maximum load conditions
Source: CONOPS Section 3.4
Priority: High
Dependencies: None
Validation Approach
Requirements validation ensures alignment with CONOPS through:
- Peer reviews
- Stakeholder assessments
- Cross-functional analysis
- Performance simulations
Common validation criteria include:
- Clarity and unambiguity
- Technical feasibility
- Cost-effectiveness
- Measurability
- Traceability to CONOPS
By following this structured approach, organizations can develop robust operational requirements that effectively bridge the gap between concept and implementation. The key is maintaining rigor while ensuring the process remains adaptable to specific project needs.
4. Performance Requirements
The transformation of operational concepts into measurable performance requirements provides the foundation for system validation and acceptance. These requirements establish clear, quantifiable metrics that define operational success across different aspects of system performance.
Key Performance Requirements by Category:
Requirement Category | Description | Transportation Example | Defense Example | Manufacturing Example |
---|---|---|---|---|
System Availability | Core uptime and reliability metrics | 99.5% service availability; Recovery < 10 mins | 99.99% combat system availability | Production line available 98% |
Response Times | Speed of system reactions and processing | Signal response < 200ms | Weapon system < 50ms | Robot control < 100ms |
Throughput Capacity | Volume handling capabilities | 30 trains per hour | 24 missions per day | 1000 units per hour |
Quality Standards | Accuracy and error tolerance levels | Position accuracy ±0.5m | Target accuracy ±0.1mrad | Defect rate < 0.1% |
Recovery Performance | Time to restore normal operations | Service restoration < 30 mins | Battle system restart < 1 min | Line restart < 15 mins |
User Efficiency | Human operator performance metrics | Operator response < 5 secs | Mission planning < 30 mins | Assembly time < 3 mins |
Scalability | Growth and peak handling capability | Peak capacity +20% | Surge capacity +50% | Production surge +30% |
Each performance requirement must be:
- Clearly defined and measurable
- Testable under operational conditions
- Aligned with system capabilities
- Traceable to operational needs
- Regularly monitored and validated
These requirements provide the baseline for system acceptance testing and ongoing performance monitoring, ensuring the implemented solution meets its intended operational objectives.
5. Operational Risk Requirements
In today’s complex operational environments, managing risk isn’t just about prevention—it’s about creating resilient systems that can adapt and respond to challenges. From manufacturing floors to defense installations, organizations must embed risk management into their operational DNA.
Safety and security form the foundation of risk requirements. Every operational system must incorporate multiple layers of protection, starting with basic safety controls and extending to sophisticated security measures. For instance, modern manufacturing plants are implementing zero-trust security architectures while maintaining traditional safety interlocks, creating a comprehensive safety-security envelope.
Business continuity has emerged as a critical focus area, particularly following recent global disruptions. Organizations are moving beyond simple backup systems to develop sophisticated resilience strategies. A European automotive manufacturer recently demonstrated this approach by implementing a flexible production system that can maintain 60% capacity even during major disruptions, setting a new standard for operational resilience.
Operational Risk in Action: The BASF Chemical Plant Integration A compelling example of comprehensive risk management comes from BASF’s recent smart factory implementation in Germany. Their approach demonstrates how modern risk requirements work in practice:
- Implemented an integrated safety-security system linking 4,000 sensors
- Achieved 99.98% uptime while maintaining zero reportable safety incidents
- Reduced emergency response times from 15 minutes to under 3 minutes
- Demonstrated how AI-powered risk prediction prevented 12 major incidents
- Resulted in 40% reduction in environmental incidents through predictive analytics
This real-world example shows how properly implemented risk requirements can transform operations while enhancing safety and efficiency.
Emergency response capabilities must be both robust and adaptable. The key is developing response systems that can scale and adjust to different types of incidents. Leading organizations are now implementing AI-assisted incident management systems that can predict and respond to emerging situations before they become critical.
Environmental and asset protection requirements have also evolved significantly. Modern operations must demonstrate not just compliance with environmental standards, but proactive environmental stewardship. This includes real-time monitoring systems and predictive maintenance programs that prevent environmental incidents before they occur.
6. Integration Requirements
Integration in modern operations goes far beyond simple system connectivity. It’s about creating a seamless operational ecosystem where information and actions flow naturally across different platforms, teams, and organizations.
Internal system integration provides the backbone of operational effectiveness. Modern operations require real-time data flow between different systems, from shop floor controls to enterprise management systems. This integration must be both robust and flexible, allowing for system updates and modifications without disrupting operations. For example, a recent aerospace manufacturer implemented a digital thread that connects design, production, and maintenance systems, reducing integration-related delays by 40%.
External integration has become increasingly critical as operations become more interconnected. Organizations must maintain secure, reliable connections with suppliers, customers, and regulatory systems while protecting sensitive information. Leading companies are adopting standardized integration frameworks that allow them to quickly establish and modify external connections while maintaining security and performance.
Human integration remains perhaps the most crucial element. Operators, maintenance teams, and management must all interact effectively with systems and each other. This requires careful attention to interface design, training systems, and documentation. Successful organizations are moving beyond traditional training approaches to implement adaptive learning systems that adjust to individual user needs and preferences.
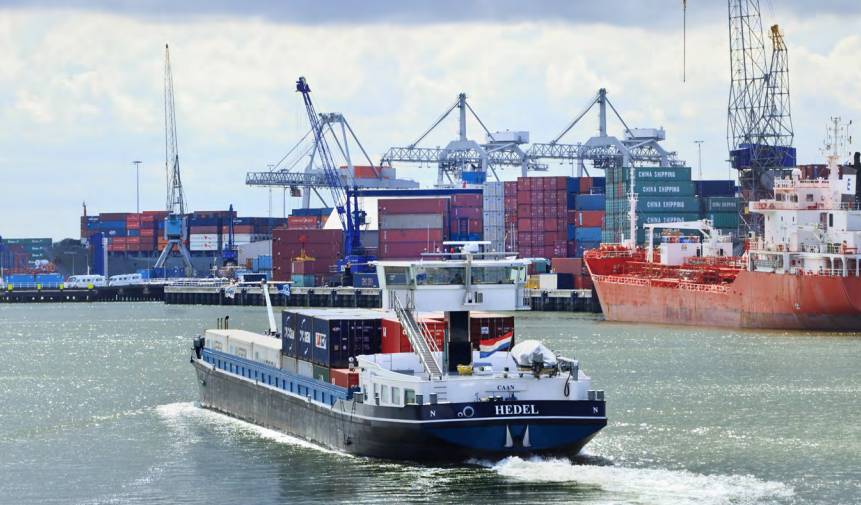
Integration Excellence: The Port of Rotterdam Digital Transformation The Port of Rotterdam’s digital transformation project provides a masterclass in modern integration requirements:
- Connected 42 different operational systems into a single digital platform
- Integrated real-time data from 1,200 vessels and 10,500 port movements monthly
- Reduced vessel waiting times by 20% through coordinated operations
- Achieved 99.99% system availability across all integrated platforms
- Demonstrated seamless integration between public and private systems
This example illustrates how well-designed integration requirements can transform complex operations across multiple stakeholders and systems.
The migration from legacy to new systems presents unique integration challenges. Organizations must maintain operational continuity while upgrading systems and processes. This often requires careful planning and staged implementation approaches. For instance, a major transit system recently completed a signaling system upgrade while maintaining full operations, achieved through careful integration planning and robust testing protocols.
Successful integration depends on clear standards, comprehensive testing, and ongoing monitoring. Organizations must establish clear metrics for integration performance and regularly assess their effectiveness. This includes not just technical metrics like system response times, but also operational metrics that measure the real-world impact of integration efforts.
7. Validation and Quality Assurance
The success of operational requirements hinges on rigorous validation and quality assurance processes. Modern validation approaches must balance thoroughness with agility, ensuring systems meet requirements without causing excessive delays or costs.
Requirements testing has evolved beyond simple checklist approaches to include continuous validation throughout the operational lifecycle. This includes automated testing frameworks, simulation-based validation, and real-world performance monitoring. Organizations are increasingly adopting “digital twin” approaches that allow them to validate changes virtually before implementing them in production.
Traceability remains essential for managing complex operational requirements. Every requirement must be traceable from its original operational need through implementation and validation. This creates a clear chain of accountability and ensures nothing is overlooked during system changes or updates.
Quality assurance processes must be dynamic and responsive to changing operational needs. Static, periodic reviews are being replaced by continuous monitoring and adaptive testing approaches that can identify and respond to issues in real-time.
Validation in Action: Tesla Gigafactory Berlin
Tesla’s Berlin Gigafactory demonstrates modern validation excellence:
- Implemented continuous validation across 2,000+ operational requirements
- Achieved 99.96% first-pass quality through AI-powered testing
- Reduced validation cycle time from weeks to hours using digital twins
- Connected 850 validation points into a single monitoring platform
- Demonstrated real-time requirement adaptation based on production needs
8. Documentation and Maintenance
Documentation of operational requirements must strike a balance between comprehensiveness and accessibility. Modern documentation approaches emphasize clear structure, regular updates, and easy access while maintaining rigorous control over critical information.
Configuration management has become increasingly important as systems become more complex and interconnected. Organizations must maintain clear records of requirement changes, system configurations, and operational modifications while ensuring this information is readily available to those who need it.
Documentation Excellence: Airbus A350 Program, Airbus’s A350 program shows best-in-class documentation and maintenance:
- Managed 120,000+ operational requirements across 40 countries
- Achieved 100% traceability of safety-critical requirements
- Reduced documentation update cycle by 65% through automated systems
- Maintained real-time requirement synchronization across 1,200 suppliers
- Demonstrated effective management of requirement changes across a 30-year lifecycle
Lifecycle management of requirements ensures they remain relevant and effective throughout the system’s operational life. This includes regular reviews, updates based on operational experience, and adaptation to changing business needs.
9. Conclusion
Effective operational requirements provide the foundation for successful system implementation and operation. Through careful attention to performance, risk, integration, validation, and documentation requirements, organizations can build systems that are both robust and adaptable to changing needs.
These requirements must be living documents that evolve with operational experience and changing business needs while maintaining clear traceability and control. Success depends on finding the right balance between rigorous control and operational flexibility, all while keeping focus on the ultimate goal: delivering reliable, efficient, and safe operations.