Welcome to the age of Industry 4.0, where the lines between the physical and digital worlds become increasingly blurred. One of the transformative technologies stirring the waters of innovation is digital twin technology.
A digital twin is the real-time virtual counterpart of a physical object, process, or service. With the seamless interplay between the virtual and physical realms, these digital replicas have become a game-changer across various industries.
One field harvesting the benefits of this technology is systems engineering. It’s a transdisciplinary and integrative approach encompassing the design, integration, and management of complex systems throughout their lifecycle.
Table of Contents
Digital Twins in Systems Engineering
By combining digital twin technology and systems engineering, we can tap into unimaginable avenues of innovation and efficiency. Moreover, coupling this technology pair within a model-based systems engineering (MBSE) framework opens the doors to streamlined development processes and reduced costs.
The interplay of digital twins, systems engineering, and digital modeling promises a digital revolution, one that could reshape the industrial horizon as we know it.
Welcome to the future of systems engineering!
The Synergy of Digital Twins and Systems Engineering
Understanding the interplay between digital twins and systems engineering is crucial for grasping the full potential of this technological partnership. While these concepts are powerful on their own, their integration creates a synergy that enhances every phase of a system’s lifecycle.
The table below illustrates how digital twins and systems engineering concepts work together across different phases of a system’s life. It demonstrates the continuous value that digital twins bring to systems engineering processes, from initial design to final decommissioning. By seeing this relationship laid out across the system lifecycle, we can better appreciate how digital twins are revolutionizing the field of systems engineering.
Each row in the table represents a phase in the system lifecycle. The columns show the role of the digital twin, the relevant systems engineering concept, and how these two elements work together to improve processes and outcomes. This holistic view highlights the transformative impact of integrating digital twins with traditional systems engineering approaches.
Phase | Digital Twin | SE Concept | How They Work Together |
---|---|---|---|
Design | Virtual prototype | Requirements management | Digital twin simulates design, allowing rapid iteration to meet changing requirements |
Development & Testing | Simulated product | Verification & Validation | Digital twin enables virtual testing, reducing physical prototyping costs and time |
Production | Virtual production line | Quality management | Digital twin optimizes manufacturing processes, ensuring consistent quality |
Operation & Maintenance | Real-time system model | Reliability & Maintainability | Digital twin predicts maintenance needs, improving system reliability |
End-of-Life | Decommissioning simulation | Lifecycle management | Digital twin aids in planning safe and efficient system retirement |
Continuous Improvement | Evolving digital model | Knowledge management | Digital twin serves as a “single source of truth,” facilitating knowledge transfer across phases |
As we can see from this table, the integration of digital twins with systems engineering processes creates a powerful framework for managing complex systems throughout their entire lifecycle. This synergy leads to more efficient design processes, reduced costs, improved quality, and enhanced decision-making at every stage.
The Intersection of Digital Twin Technology and Systems Engineering
Digital twin technology marries perfectly with the objectives of MBSE. Digital twins in an MBSE framework can effectively simulate ‘what-if’ scenarios under the close supervision of systems engineers. Data captured from the physical counterpart is relayed to the digital twin, providing real-time insights to track and predict performance.
Furthermore, MBSE tools and data acquisition instruments interlink to create a robust communication channel between the digital twin, the physical system, and the MBSE system lifecycle. This integration stands as a testament to the symbiotic relationship between systems engineering and digital twins.
Employing digital twins within the MBSE framework delivers an interconnected platform for engineering processes. The bond created between the digital twin technology and MBSE creates a fertile ground for innovation and has potential to revolutionise the future of systems engineering.
Recommended Further Reading Amazon BooksThe Advantages of Digital Twins for Systems Engineering
The application of Digital Twin technology in Systems Engineering projects has a profound impact on driving success, boosting efficiency and reducing costs. The efficacy of such a blend is not simply bound by theoretical conjectures; well-documented projects provide testament to these assertions.
When a digital twin is efficiently integrated within the systems engineering process, the benefits become evident on every level – design, management and the interplay with various stakeholders who influence the project. As a fundamental subset of the Industry 4.0, Digital Twins harvest data from a host of sources, including internet-enabled sensors, drones, cameras and other advanced devices. This data enables simulation of system behaviours, thereby facilitating iterative design and progressive improvements.
Consider a real-world example: a technology firm manufactures a computer and creates a digital twin linked to the service history, manufacturing process, interconnected device and internet-enabled sensor data, projected failure modes, and configuration-specific simulation models of its physical counterpart. By running simulations and comparing outputs to real-world results, the firm can gain insightful data about the prototype. This detailed analysis underpins impressive advancements in product development and operational efficiency, leading to unprecedented levels of predictive maintenance.
Unlocking New Opportunities
Moreover, the use of digital twin technology in MBSE frameworks can discover new application opportunities and revenue streams. It offers a chance to evaluate different versions of the system to deduce the most efficient iteration. In tandem with advanced technologies like machine learning and AI, massive volumes of data can be meticulously analysed to identify and benefit from fresh opportunities and revenue streams.
Additional Benefits
Other advantages of implementing digital twins in system engineering frameworks include enhanced traceability due to the digital thread, remote troubleshooting, and efficient diagnostic testing. The digital thread interlinking the digital twin with its physical counterpart allows an integral connection between life-cycle phases. Similarly, diagnostic testing becomes straightforward when the digital twin mirrors its physical counterpart’s state accurately.
The merger of digital twins and systems engineering, specifically within the MBSE architecture, brings forth a suite of advantages, pushing the boundaries of innovation and leading the way in the digital revolution.
Industry | Digital Twins in Systems Engineering | Future Opportunities |
---|---|---|
Aerospace | Rolls-Royce has successfully implemented digital twin technology to create virtual replicas of their aircraft engines. This has allowed for detailed analysis and monitoring of engine performance during operating conditions, dramatically reducing the need for unscheduled maintenance. | A recent NASA report has outlined the potential application of digital twins in the design and operation of spacecraft for future deep-space missions. The ability to simulate unforeseen challenges and test new solutions could dramatically reduce the cost and risk of these ventures. |
Healthcare | Philips has pioneered the use of digital twins in telemedicine, with virtual patient models showing accurate health status and progression in real time. This has significantly enhanced the prediction of patient outcomes and personalised treatment plans. | A research in Nature Digital Medicine journal suggests that digital twins could revolutionise drug development by predicting individual patient responses, potentially accelerating the creation of new medicines and reducing the reliance on costly and time-consuming clinical trials. |
Manufacturing | General Electric has effectively employed digital twins in modelling its manufacturing systems, leading to the early detection of potential failures and optimisation of manufacturing processes. | As outlined by McKinsey & Company, digital twins could play a crucial role in future supply chain optimisation. By creating a virtual copy of the entire supply chain, companies can perform predictive analysis, detect bottlenecks, and optimise resources in real time. |
Energy | Schneider Electric leverages digital twin technology in managing and maintaining complex energy distribution grids. This has resulted in improved system resilience and a decrease in energy delivery interruptions. | Gartner predicts that by 2025, digital twins will be integrated with AI to provide advanced energy management. By optimising the distribution and storage of renewable energy, it will be possible to create more sustainable and resilient energy systems. |
Automobile | Tesla uses digital twins to replicate critical vehicle systems, such as its Battery Management System (BMS). This allows engineers to simulate different operating scenarios and optimise the system design for enhanced safety and performance. | As per report by Capgemini, digital twins can be used to simulate autonomous driving scenarios with AI. This could expedite the creation of advanced self-driving technology while also reducing the risks associated with real-world testing. |
Agriculture | John Deere is using digital twin technology to optimise its large farming machinery. This includes sensor data and detailed models to predict machine behaviour, improving maintenance schedules and reducing downtime. | A report by Capgemini suggests that digital twins could revolutionise yield predictions, crop disease management, and precision farming. The creation of ‘digital farm’ models could allow farmers to optimise their use of resources and predict crop yields more accurately. |
Construction | Siemens uses digital twins to optimise the energy efficiency of buildings under construction. This allows designers to simulate the effects of different energy-saving measures and select the most effective solution. | The University of Cambridge believes that future construction projects could increasingly rely on digital twins, not only to predict the performance of individual systems such as HVAC but also forecast entire lifecycle costs and environmental impacts of buildings. |
The Future of Digital Twins in Systems Engineering
As we delve further into the realm of Industry 4.0, digital twin technology is setting a steady course towards being a cornerstone in the framework of Model-Based Systems Engineering (MBSE). Beyond embracing the full system lifecycle, digital twins are paving the way for MBSE to infiltrate new markets, such as real estate, manufacturing and construction sectors. Indeed, systems engineering underpinned by the technology of digital twins is beginning to shape the future of the digital revolution.
In an MBSE framework, digital twins can be employed in a myriad of ways, ranging from initial engineering concepts to smart manufacturing and testing. Even aspects of system maintenance, such as condition-based maintenance strategies, make extensive use of digital twin technology. The wide range of applications suggests a fast-growing dependency and trust in the robustness of the technology.
Recommended Further Reading Amazon BooksDigital Twins in Real Estate and Construction
Real estate and construction industries are other domains anticipated to experience the impact of digital twin proliferation. The need for real-time systems data access to streamline operations and enable adaptive energy management solutions make these sectors ripe for the introduction of digital twin technologies.
Transition from Schedule-Based to Condition-Based Maintenance
Another pivotal evolution is the shift from schedule-based to condition-based maintenance in many organisations. This transition is largely facilitated by the ability of digital twins to reflect the real-world condition of their physical system counterparts. This allows maintenance teams to accurately predict and schedule repairs, thus improving organisational efficiency.
Digital Twins as the Single Source of Truth
The digital thread enables the accurate transfer of data across the continuum of a system’s lifecycle. Systems engineers can gauge performance meticulously and isolate technical risks, thanks to digital twins. With the adoption of MBSE frameworks, digital twins are predicted to emerge as the single authoritative source of truth about the behaviour of complex systems throughout their life.
As we stand at the cusp of the Fourth Industrial Era, the fusion of digital twins with systems engineering is sure set to redefine the parameters of the digital landscape, leading us headfirst into the digital revolution and beyond.
It’s apparent that the application of digital twins in systems engineering signifies a transformative shift to a multi-dimensional, data-centric approach. This paradigm, where digital replicas mirror their physical counterparts, is shaping the future of industries globally – a digital revolution indeed.
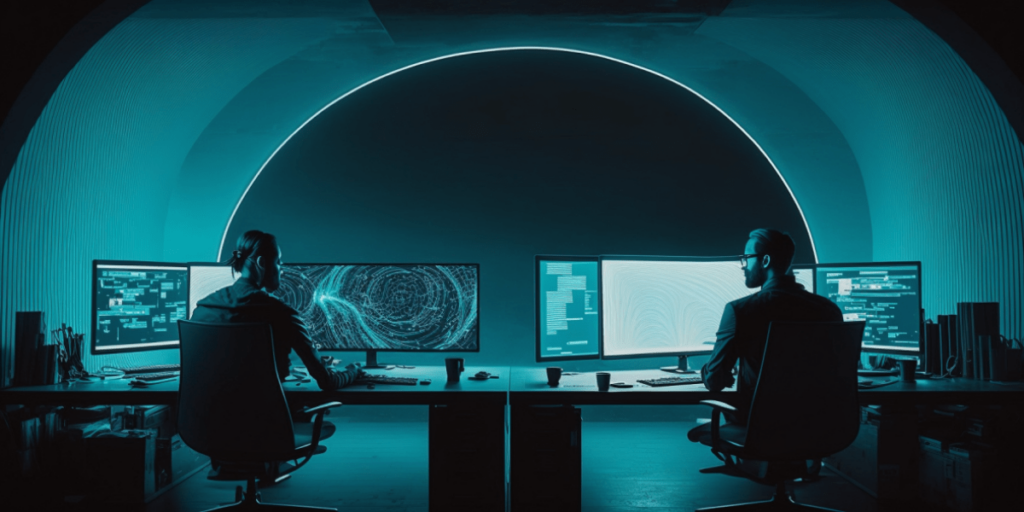
Understanding Model-Based Systems Engineering (MBSE)
Model-based Systems Engineering (MBSE) is an approach that uses models as the primary medium for information exchange rather than relying on traditional document-centered methods. Distinguished by its focus on digital modeling and the application of formalized modeling methods, MBSE is becoming integral in numerous engineering fields, including systems engineering.
This dynamic shift from document-centricity to model-centricity dramatically alters the landscape of systems engineering. Documentation, while still important, often becomes unmanageably bulky and complex, particularly in large-scale projects. With MBSE, the reliance on extensive document trails becomes replaced by graphic or computational models that simplify complex systems and streamline communication among stakeholders.
Utilising digital modeling environments within MBSE has shown to significantly enhance project outcomes and facilitate more efficient implementation of complex tasks. It is suggested that the application of solid digital modeling techniques within MBSE can lead to a reduction of up to 55% in total development costs.
Modeling Languages in MBSE
At the heart of MBSE lie the modeling languages, enabling rich, detailed visual and semantic representation of the intended system. Primarily, two forms of modeling languages are employed – general-purpose and specialised. Systems Modeling Language (SysML) and Unified Modeling Language (UML) are leading examples of general-purpose modeling languages, while the Architecture Analysis Design Language (AADL) is commonly used as a specialised modeling language.
Within the broader context of systems engineering, MBSE integrates three key concepts – models, systems thinking, and systems engineering. The models serve as simplified versions of complex entities, making them easy to understand and work with. Systems thinking provides a systemic framework for examining systems as part of larger, integrated wholes, offering a more holistic and comprehensive view. Lastly, systems engineering helps in structuring these insights to facilitate the successful operation and retirement of engineered systems.
Recommended Future Learn Short CoursesDigital Twins: A Powerful Tool for Modern Engineering
Digital Twins, backed by model-based systems engineering (MBSE), are emerging as an unprecedented tool in modernising system design and maintenance procedures. They allow engineers to simulate, analyse, and optimise system performance influencing outstanding outcomes in terms of efficiency, reliability, and cost savings.
Embracing the Digital Future
The digital future beckons us to lean into sophisticated digital modelling techniques. Embracing these forward-thinking practices enables us to fully harness the potential of Digital Twins, transitioning seamlessly between physical and virtual realms throughout the system’s lifecycle. It’s crucial for industries to adapt and adopt these revolutionary shifts, thereby creating an environment ripe for innovation and growth.
As our technological landscape continues to evolve, Digital Twins and Systems Engineering meld seamlessly, setting a new paradigm for how we comprehend, interact with, and optimise complex systems. Effectively, it is an invitation to join the forefront of this digital revolution and engineer a future that is synergistic, streamlined, and sustainable.
Comment on “Digital Twins in Systems Engineering: A Digital Revolution”