The landscape of industrial control systems is evolving at a rapid pace. With the rapid progression of technology, the tasks that operators need to execute are becoming increasingly complex. To navigate this complexity, a flexible and user-friendly control system is essential. Enter the world of Human Machine Interface (HMI) – a technological innovation that is revolutionising the way we interact with machinery.
Table of Contents
Understanding HMI
HMI, or Human Machine Interface, is essentially a user interface or dashboard. It allows a user to engage with a machine, computer program, or system. This term generally applies to any screen a user employs to interact with a device. However, it’s most commonly used in industrial contexts. Human Machine Interfaces offer real-time data, and give users the ability to control machinery through a graphical user interface.
Think of it like driving a car. You’re in control of the engine, steering, lights, air conditioning, stereo, among other things. You don’t directly interact with each of these parts. Instead, you use controls and feedback instruments such as the speedometer, accelerator, and steering wheel. These are akin to the car’s HMI, offering a user-friendly interface between you and the vehicle’s complex machinery.
In an industrial environment, an HMI might take the form of a standalone screen, a dashboard attached to a machine, or even a tablet. No matter what it looks like, an HMI’s main purpose is to help users visualise operational data and control machinery.
The Diverse Applications of HMI
Human Machine Interfaces (HMIs) find extensive use across numerous sectors. These include manufacturing, energy, water, wastewater management, buildings, and transport. For system integrators, operators, and engineers, especially those involved with process control systems, they’re a common tool.
Depending on the machine or system complexity, and the specific functions it must perform, an HMI’s sophistication may vary. For example, an HMI might monitor a single machine or control and oversee an entire plant’s operations.
When a Supervisory Control and Data Acquisition (SCADA) system interacts with Programmable Logic Controllers (PLCs) and input/output sensors, it gathers equipment operation information. This data is then displayed on an HMI. Presented in various visual formats like graphs or charts, the data becomes easy to understand.
As the Internet of Things (IoT) extends its reach into industrial facilities, HMIs are gaining increased relevance. They offer a centralised hub for data and control, allowing users to view and control various connected devices within a facility.
Human Machine Interfaces (HMIs) are utilized across a wide array of industries. Here are some examples:
Manufacturing
In manufacturing, HMIs are often used to control production lines. They allow operators to monitor real-time data about the operation of machines, and to control these machines directly from the interface.
Energy
Energy companies use HMIs to monitor and control power generation equipment. This could be in a traditional power station or in renewable energy generation, such as wind turbines or solar panels.
Water and Wastewater Management
Human-Machine Interfaces (HMIs) play a crucial role in water treatment plants. Primarily, they monitor and control the diverse processes involved in water purification. Likewise, these systems are vital in wastewater management, overseeing the treatment of sewage.
Buildings
In smart buildings, we utilise Human Machine Interfaces (HMIs) to manage various systems. These include heating, ventilation, and air conditioning (HVAC), lighting, and security systems. Moreover, these HMIs allow us to monitor energy consumption. Consequently, we can control these systems to enhance energy efficiency.
Transportation
HMIs play a vital role in transportation. For instance, traffic control centres utilise them to manage and regulate traffic flow. Additionally, in railway systems, HMIs are instrumental in controlling signalling systems. Moreover, they provide critical monitoring of train and track conditions.
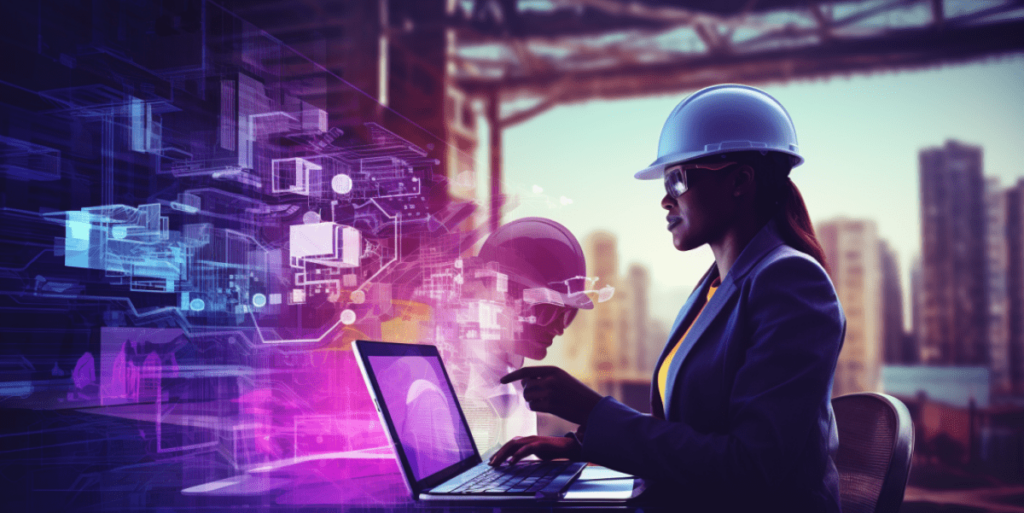
Integrating HMI into Your Systems
Incorporating an HMI solution into your current systems can be simple, especially with modern platforms. These platforms support numerous communication protocols and are compatible with key operating systems. Often, you can access them via a web server or HTML5 web engine. This allows for remote access and real-time updates for all users.
A significant advantage of an HMI system is the customisation options it offers to users. Users have the freedom to create and position widgets as per their needs. They can also control the visibility of different elements either for security reasons or to design role-specific dashboards. This degree of customisation facilitates user-friendly dashboards that only display information relevant to each user.
The Advantages of Using HMI
HMI usage in industrial settings comes with countless benefits. These include increased operational visibility, enhanced efficiency, reduced downtime, improved user-friendliness, and a unified equipment control system.
Human Machine Interfaces (HMIs) offer exceptional operational visibility. They allow real-time equipment or facility performance monitoring from a single dashboard. Consequently, this leads to increased productivity and faster issue resolution.
Moreover, HMIs boost efficiency. They provide constant real-time data access, enabling production monitoring and adjustments in response to demand fluctuations. Particularly when paired with data analysis technologies, data visualisation can pinpoint operational efficiency improvement areas.
HMIs also significantly cut downtime. Alerts on a central dashboard enable quick responses to problems, stopping minor issues from escalating into major problems causing significant downtime.
Furthermore, HMIs enhance control system usability. They present data in a visually appealing, easily understandable format, facilitating quicker and easier user interpretation. Users can also personalise their dashboards to their needs and preferences, further enhancing usability.
Lastly, HMIs provide a unified equipment control system. All equipment can be controlled from the same platform, simplifying operator learning and providing a comprehensive facility overview.
The Future of Human Machine Interface (HMI)
As technology progresses, Human Machine Interface (HMI) consistently evolves. The rise of high-performance HMIs is noteworthy. These systems focus on drawing user attention to crucial information. Furthermore, multi-touch screens, remote surveillance, and cloud-based systems are gaining popularity.
Looking ahead, we anticipate the use of advanced data analytics and artificial intelligence. They will extract insights from data, communicated to users via HMIs. Additionally, Augmented Reality (AR) and Virtual Reality (VR) technologies may merge into HMIs. This integration will produce more effective visual aids for users.
In summary, HMI stands as a potent tool in the industrial control systems sphere. It bridges the gap between operators and complex machinery with a user-friendly interface. This connection allows real-time monitoring and control of operations. As technology progresses, the role of Human Machine Interface in industrial processes will undoubtedly become increasingly significant.